12 Effective Strategies to Reduce Inventory Costs and Improve Cash Flow
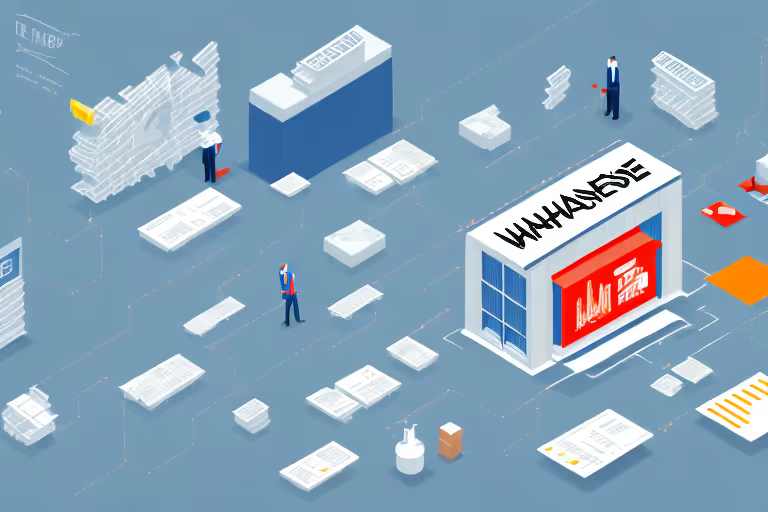
In today's competitive business landscape, it is crucial for companies to find ways to reduce inventory costs and improve cash flow. By implementing effective strategies, businesses can optimize their supply chain, streamline processes, and mitigate risks. In this article, we will explore twelve proven strategies that can help you achieve these goals.
Optimizing Supply Chain Costs
In today's competitive business landscape, optimizing supply chain costs is crucial for companies to remain profitable and gain a competitive edge. By closely examining the impact of production changes, streamlining ordering processes, mitigating shortage costs, minimizing shipping and transportation expenses, managing carrying costs, assessing and mitigating inventory risk costs, optimizing labor costs, understanding and managing capital costs, evaluating inventory valuation methods, and calculating and analyzing the cost of goods sold, companies can make informed decisions and achieve cost savings throughout their supply chain.
Analyzing the Impact of Production Changes on Costs
To reduce inventory costs, it is important to closely examine the impact of production changes. By analyzing the costs associated with different production methods and identifying opportunities for improvement, companies can make informed decisions about how to streamline their operations. This analysis can help identify bottlenecks, eliminate waste, and optimize resource allocation.
For example, companies can analyze the cost implications of switching to more efficient production technologies or implementing lean manufacturing principles. By identifying areas where production costs can be reduced, companies can achieve significant savings in their supply chain.
Furthermore, analyzing the impact of production changes on costs can also help companies identify opportunities for automation and process optimization. By leveraging technology and implementing efficient production processes, companies can reduce labor costs, improve productivity, and minimize errors.
Streamlining Ordering Processes to Reduce Costs
One of the key areas where inventory costs can be reduced is in the ordering process. By implementing efficient order management systems and processes, companies can minimize errors, improve accuracy, and optimize inventory levels. Automation and integration of ordering systems can also lead to significant cost savings by eliminating manual tasks and reducing administrative burdens.
Streamlining ordering processes involves optimizing the entire order-to-delivery cycle. This includes improving demand forecasting accuracy to avoid overstocking or understocking, implementing vendor-managed inventory systems to optimize replenishment, and leveraging electronic data interchange (EDI) to automate order processing and reduce paperwork.
Additionally, companies can explore collaborative planning, forecasting, and replenishment (CPFR) initiatives with key suppliers and customers. By sharing information and aligning demand and supply plans, companies can reduce lead times, improve order fulfillment rates, and minimize inventory holding costs.
Mitigating Shortage Costs through Effective Inventory Management
Shortages can significantly impact a company's bottom line. By implementing effective inventory management practices, companies can minimize the risk of shortages and avoid the associated costs. This includes accurate demand forecasting, real-time visibility of inventory levels, and proactive replenishment strategies. By having the right products in stock at the right time, companies can avoid costly expedited shipping, lost sales, and dissatisfied customers.
Effective inventory management involves optimizing inventory levels based on demand patterns, lead times, and service level targets. This can be achieved through the use of inventory optimization software, which takes into account various factors such as demand variability, lead time variability, and desired service levels.
Furthermore, companies can implement cross-docking strategies to minimize storage costs and improve order fulfillment speed. By receiving products from suppliers and immediately shipping them to customers without storing them in a warehouse, companies can reduce inventory holding costs and improve overall supply chain efficiency.
Minimizing Shipping and Transportation Expenses
Shipping and transportation expenses can quickly add up and significantly impact inventory costs. To reduce these costs, companies can explore various strategies, such as optimizing shipping routes, leveraging technology to consolidate shipments, and negotiating favorable contracts with carriers. Additionally, implementing efficient warehouse layout and picking procedures can minimize time spent on transportation activities and reduce associated costs.
Optimizing shipping routes involves analyzing transportation networks, considering factors such as distance, traffic patterns, and carrier capabilities. By identifying the most efficient routes, companies can reduce transportation costs and improve delivery speed.
Consolidating shipments involves combining multiple smaller shipments into a larger shipment. This not only reduces transportation costs but also minimizes the environmental impact of transportation by reducing fuel consumption and emissions.
Furthermore, companies can implement efficient warehouse layout and picking procedures to minimize transportation-related costs. By organizing products in a logical and efficient manner, companies can reduce the time and effort required to pick, pack, and ship orders, resulting in cost savings and improved customer satisfaction.
Managing Carrying Costs for Efficient Inventory Control
Carrying costs, including warehousing, insurance, and obsolescence, can have a substantial impact on inventory expenses. To reduce these costs, companies can implement efficient inventory control practices, such as ABC analysis to identify high-value items and prioritize storage space, and just-in-time inventory management to minimize storage requirements. By optimizing inventory levels and reducing carrying costs, companies can free up cash flow and improve profitability.
ABC analysis involves categorizing inventory items based on their value and importance. This allows companies to allocate storage space and resources more effectively, ensuring that high-value items are given priority. By focusing on high-value items, companies can reduce carrying costs and improve overall inventory control.
Just-in-time inventory management involves receiving inventory from suppliers just in time for production or customer demand. This approach minimizes the need for extensive warehousing and reduces the risk of inventory obsolescence. By closely coordinating with suppliers and customers, companies can achieve significant cost savings and improve overall supply chain efficiency.
Assessing and Mitigating Inventory Risk Costs
Inventory risk costs, such as theft, damage, and obsolescence, can have a significant impact on the bottom line. To mitigate these costs, companies can implement robust inventory control measures, such as security systems, regular audits, and strict quality control processes. Additionally, proactive monitoring of market trends and product lifecycle can help identify potential risks and enable companies to take timely action.
Implementing security systems, such as surveillance cameras and access control measures, can deter theft and unauthorized access to inventory. Regular audits and inventory reconciliation processes can help identify discrepancies and minimize the risk of inventory shrinkage. Strict quality control processes can ensure that inventory is properly handled and stored, reducing the risk of damage or spoilage.
Furthermore, companies can closely monitor market trends and product lifecycle to identify potential risks. By staying ahead of changing customer preferences and technological advancements, companies can proactively adjust their inventory levels and product offerings, minimizing the risk of obsolescence and associated costs.
Optimizing Labor Costs in the Supply Chain
Labor costs play a significant role in inventory expenses. By optimizing labor utilization and productivity, companies can reduce costs without compromising operational efficiency. This can be achieved through effective workforce planning, training, and cross-training programs. Additionally, leveraging automation and technology in areas such as order picking and inventory tracking can help streamline operations and reduce labor-intensive tasks.
Effective workforce planning involves aligning labor resources with demand patterns and operational requirements. By accurately forecasting labor needs and adjusting staffing levels accordingly, companies can avoid overstaffing or understaffing, resulting in cost savings.
Investing in training and cross-training programs can enhance employee skills and versatility, enabling them to perform a wider range of tasks. This improves operational flexibility and reduces the need for additional labor resources, resulting in cost savings.
Furthermore, companies can leverage automation and technology to streamline labor-intensive tasks. For example, implementing automated order picking systems can significantly reduce the time and effort required to fulfill customer orders. Similarly, using barcode or RFID technology for inventory tracking can improve accuracy and efficiency, reducing the need for manual inventory checks.
Understanding and Managing Capital Costs in Inventory Management
Capital costs, including the cost of financing inventory, are an important consideration in inventory management. By understanding the impact of capital costs on the overall cost structure, companies can make informed decisions about inventory levels, financing options, and cash flow management. Implementing effective inventory valuation methods, such as the weighted average or specific identification, can also help ensure accurate costing and improve decision-making.
Understanding capital costs involves considering the cost of capital, which includes interest expenses and the opportunity cost of tying up funds in inventory. By analyzing the cost of capital and comparing it to the potential return on investment from inventory, companies can determine the optimal inventory levels and financing options.
Implementing accurate inventory valuation methods is essential for accurate costing and decision-making. The weighted average method calculates the average cost of inventory based on the weighted average of the costs of all units in stock. The specific identification method assigns costs to individual units based on their actual cost. Choosing the most appropriate inventory valuation method depends on factors such as the nature of the products, cost fluctuations, and accounting requirements.
Evaluating Inventory Valuation Methods for Accurate Costing
Accurate costing is essential for making informed decisions about inventory management. Companies should evaluate different inventory valuation methods, such as FIFO (first in, first out), LIFO (last in, first out), and average cost, to determine the most suitable approach for their business. Accurate costing provides a clear picture of inventory profitability, helps optimize pricing strategies, and enables effective budgeting and financial planning.
The FIFO method assumes that the first units purchased or produced are the first ones sold or used. This method reflects the actual flow of inventory and is commonly used when inventory costs are rising. The LIFO method assumes that the last units purchased or produced are the first ones sold or used. This method is commonly used when inventory costs are falling. The average cost method calculates the average cost of all units in stock and is often used when inventory costs are relatively stable.
Choosing the most appropriate inventory valuation method depends on factors such as tax implications, cost fluctuations, and financial reporting requirements. By evaluating different methods and considering the specific characteristics of their inventory, companies can ensure accurate costing and make informed decisions about inventory management.
Calculating and Analyzing Cost of Goods Sold
The cost of goods sold (COGS) is a critical metric in inventory management. By accurately calculating and analyzing COGS, companies can gain valuable insights into their cost structure and profitability. This information can help identify areas of improvement, optimize pricing strategies, and support effective decision-making. Timely and accurate calculation of COGS is crucial for financial reporting and enables businesses to evaluate their performance against industry benchmarks.
Calculating COGS involves considering the direct costs associated with the production or purchase of goods, such as raw materials, labor, and overhead expenses. By accurately tracking these costs and allocating them to the corresponding units sold, companies can determine the true cost of goods sold.
Analyzing COGS allows companies
Strategies for Cost-Effective Supply Chain Management
Centralizing Purchasing to Optimize Costs
Centralizing purchasing activities can help companies optimize costs by leveraging economies of scale, negotiating bulk discounts, and reducing duplication of effort. By consolidating purchasing power, companies can streamline supplier relationships, improve sourcing strategies, and negotiate more favorable terms. Additionally, centralization allows for better coordination and standardization of processes, resulting in improved efficiency and cost savings.
Building a Diverse Supplier Network for Cost Reduction
A diverse supplier network can provide a competitive advantage by offering cost-effective options and reducing reliance on single suppliers. By identifying and partnering with a diverse range of suppliers, companies can leverage competition to negotiate better prices, access innovative products, and mitigate supply chain risks. Collaboration and long-term partnerships with suppliers can lead to mutual benefits, increased flexibility, and lower costs.
Shortening Production Cycles for Efficiency and Cost Savings
Shortening production cycles can have a significant impact on both efficiency and cost savings. By implementing lean manufacturing principles, streamlining processes, and minimizing non-value-added activities, companies can reduce lead times, optimize resource utilization, and improve overall productivity. This results in lower production costs, reduced inventory holding, and improved cash flow.
Exploring Cross-Docking Services for Streamlined Operations
Cross-docking is a logistics strategy that involves transferring goods directly from inbound to outbound transportation without storing them in a warehouse. This approach eliminates the need for warehousing and reduces handling costs, inventory holding, and associated risks. By exploring cross-docking services and leveraging technology for real-time tracking and coordination, companies can streamline operations, improve order fulfillment speed, and reduce overall supply chain costs.
In conclusion, reducing inventory costs and improving cash flow are essential for the success and profitability of any business. By implementing the twelve effective strategies discussed in this article, companies can optimize their supply chain, streamline processes, and mitigate risks. These strategies can help businesses achieve a competitive edge, maximize profitability, and ensure long-term sustainability in today's dynamic market.