A Comprehensive Guide to Understanding Optimum Stock Levels
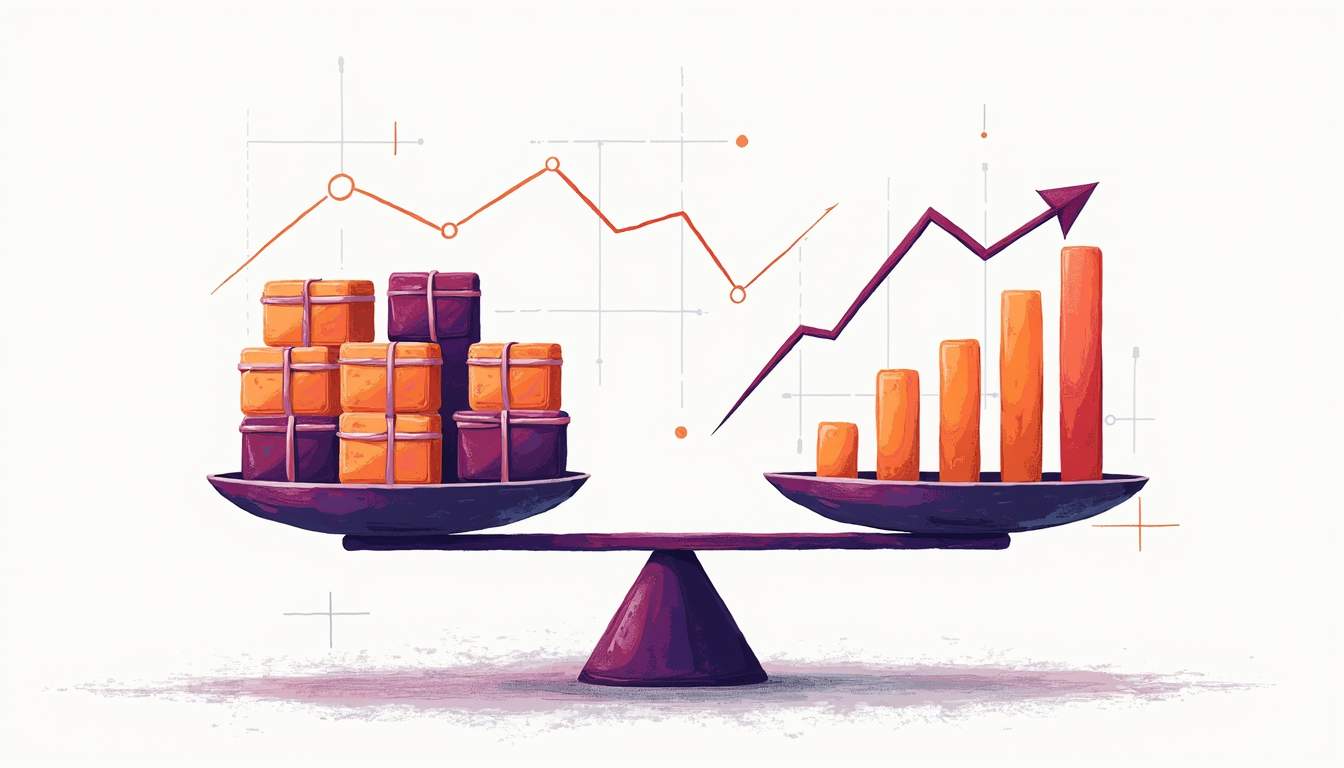
In the dynamic world of inventory management, understanding optimum stock levels is crucial for maintaining efficiency and fulfilling customer demands. This guide aims to enlighten you on the key elements and considerations that shape optimum stock levels, providing strategies to fine-tune your inventory practices and keep your business thriving.
Understanding Optimum Stock Levels
Optimum stock levels refer to the ideal quantity of stock a business should maintain to minimize costs while ensuring product availability. Striking the right balance between having enough inventory to meet customer needs and avoiding excess stock that ties up capital is a challenge all businesses face. This balance is crucial not only for operational efficiency but also for maintaining customer satisfaction, as stockouts can lead to lost sales and diminished brand loyalty.
When determining optimum stock levels, several factors come into play, including demand variability, lead times from suppliers, and storage costs. Each business must analyze its unique circumstances and market conditions to establish what "optimum" means for them. For instance, a retailer in a seasonal market may need to adjust their stock levels significantly during peak seasons, while a manufacturer might focus on maintaining steady levels throughout the year to ensure production continuity.
Defining Optimum Stock Level: Key Concepts
At its core, the optimum stock level is determined by three essential elements: demand forecasting, inventory turnover rates, and service level requirements. Understanding these components can help businesses manage their inventories effectively. Demand forecasting, for example, is not merely about predicting sales; it also involves analyzing market trends, customer behavior, and even economic indicators that might influence purchasing patterns.
Demand forecasting predicts future product demand based on historical data, seasonal trends, and market analysis. Combining accurate forecasting with appropriate inventory turnover rates—how frequently stock is replenished—can enhance cash flow and reduce storage costs. High turnover rates typically indicate efficient inventory management, but they also require businesses to stay agile and responsive to market changes. Furthermore, companies must consider the implications of lead times from suppliers, as longer lead times may necessitate higher stock levels to prevent disruptions in supply.
Service level requirements pertain to the desired level of product availability to meet customer expectations. Balancing these concepts leads to a clear understanding of what an optimum stock level looks like for any given business. A company that prioritizes customer satisfaction may opt for higher stock levels to ensure that popular items are always available, while another that focuses on cost efficiency might maintain lower levels but risk occasional stockouts. This strategic decision-making process is essential for aligning inventory practices with overall business goals and customer needs.
The Role of Safety Stock in Inventory Management
Safety stock serves as a buffer against demand fluctuations and supply chain disruptions. Maintaining safety stock ensures that a business can continue operating smoothly in the face of unexpected changes. This is particularly critical in industries where customer expectations for timely delivery are high, such as e-commerce and retail. A well-managed safety stock not only helps in meeting customer demands but also plays a vital role in enhancing a company's reputation for reliability and service quality.
The amount of safety stock needed varies from one business to another and is influenced by factors such as lead time variability and demand uncertainty. For instance, seasonal fluctuations can significantly impact demand, necessitating a higher safety stock during peak periods. Additionally, external factors such as geopolitical events, natural disasters, or supplier issues can disrupt supply chains, making it essential for businesses to adjust their safety stock levels accordingly. Calculating the correct safety stock can mitigate risks associated with inventory shortages and help maintain customer satisfaction, ultimately leading to increased sales and customer loyalty.
Calculating Safety Stock for Optimal Performance
To calculate safety stock effectively, businesses often consider the standard deviation of customer demand and lead time. Compiling this data allows for a more accurate estimate of the necessary buffer stock needed to keep operations running efficiently. It's important to note that relying solely on historical data may not always reflect future demand accurately, especially in rapidly changing markets. Therefore, incorporating market trends and forecasts into the safety stock calculation can provide a more holistic view of inventory needs.
One widely used formula in safety stock calculation is:
- Determine the average lead time and the average daily demand.
- Calculate the standard deviation for both lead time and demand.
- Apply the formula: Safety Stock = Z-score * Standard Deviation of Demand during Lead Time.
Where Z-score corresponds to the desired service level. This systematic approach enables businesses to establish safety stock levels tailored to their unique operations. Furthermore, businesses can enhance their inventory management by utilizing advanced analytics and inventory management software, which can automate the calculation process and provide real-time insights into stock levels. By leveraging technology, companies can not only optimize their safety stock but also improve overall inventory turnover rates, reducing holding costs while ensuring product availability.
Managing Excess Inventory: Finding the Right Stock Levels
Excess inventory can be detrimental, leading to increased holding costs, wasted resources, and potential obsolescence. It is crucial to identify and address excess stock proactively to maintain optimum inventory levels. The financial implications of carrying excess inventory can be significant, affecting cash flow and overall profitability. Businesses must be vigilant in monitoring their stock levels to avoid the pitfalls associated with surplus items.
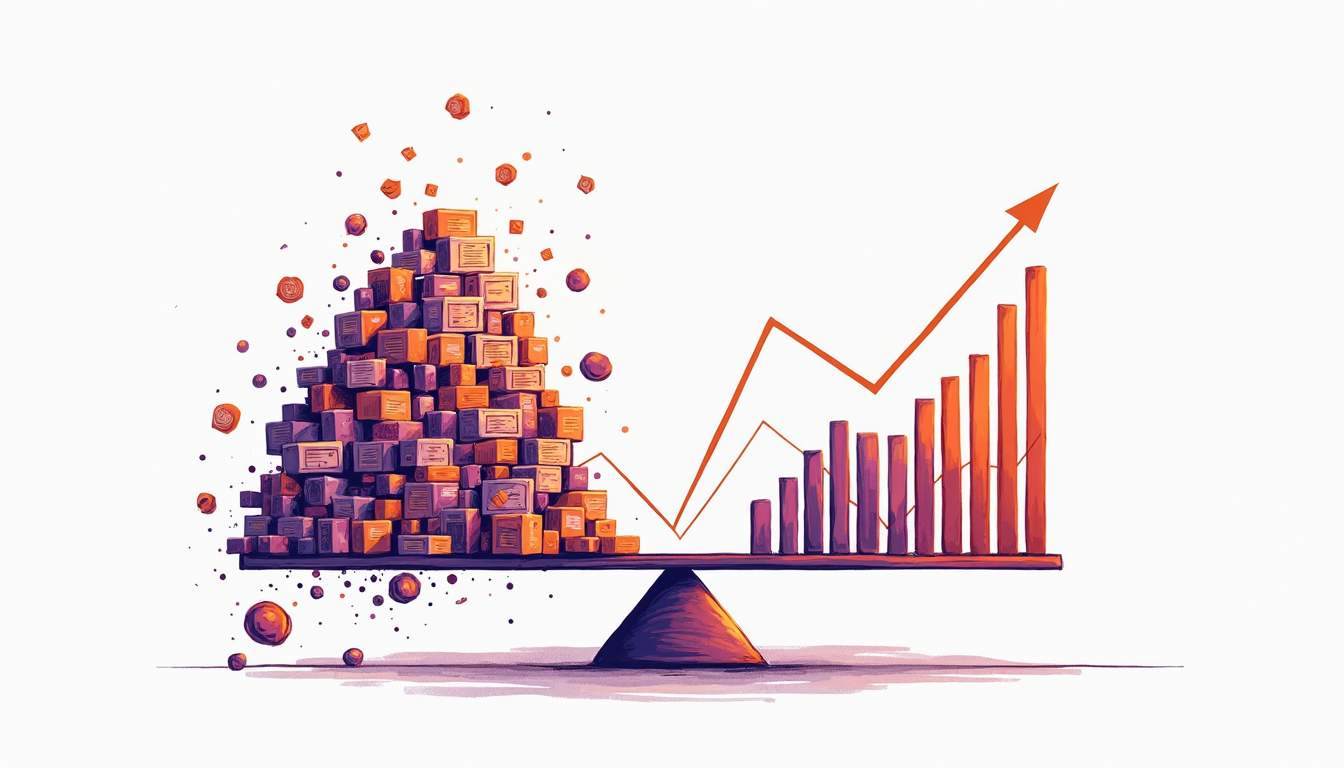
Understanding the underlying causes of excess inventory—such as overproduction, inaccurate forecasting, or changes in customer preferences—allows businesses to implement effective strategies to combat this issue. For instance, shifts in consumer behavior can result from various factors, including economic conditions, seasonal trends, or emerging technologies. By staying attuned to these changes, businesses can better align their inventory strategies with market demands, ensuring they remain competitive and responsive.
Strategies for Reducing Excess Inventory
There are several effective strategies for managing and reducing excess inventory:
- Conduct Regular Inventory Audits: Periodically review your inventory to identify slow-moving and obsolete items. These audits can reveal patterns in sales and stock turnover, enabling businesses to make informed decisions about which products to phase out or promote.
- Implement Just-In-Time (JIT) Practices: Streamline operations by only ordering stock as it’s needed for production or sales. This approach minimizes storage costs and reduces the risk of holding outdated inventory, fostering a more agile supply chain.
- Run Promotions or Discounts: Encourage sales of excess inventory through promotional offers, helping to clear stock while generating revenue. Seasonal sales, bundle deals, or loyalty discounts can attract customers and incentivize them to purchase items that may otherwise sit unsold.
- Enhance Demand Forecasting: Use advanced analytics tools to improve demand visibility and adapt more swiftly to market changes. By leveraging data analytics, businesses can gain insights into customer buying patterns, allowing for more accurate predictions and better inventory management.
By employing a mix of these strategies, businesses can eliminate excess inventory while maintaining optimum stock levels effectively. Additionally, fostering a culture of continuous improvement within the organization can help teams stay proactive in managing inventory. Regular training and workshops on inventory management best practices can equip employees with the skills needed to identify potential issues before they escalate, ensuring that the company remains agile and responsive to market dynamics.
Best Practices for Maintaining Ideal Inventory Levels
Maintaining ideal inventory levels requires a combination of regular monitoring and proactive management. Following best practices can help streamline processes and enhance overall inventory effectiveness. An efficient inventory system not only minimizes costs associated with overstocking but also ensures that customers receive their products on time, thereby improving satisfaction and loyalty.
Key best practices include:
- Establish Clear Reorder Points: Identify the minimum levels of stock needed before reordering, ensuring timely restocking. This practice helps prevent stockouts that can lead to lost sales and dissatisfied customers.
- Utilize Inventory Management Software: Leverage technology to track inventory in real-time and automate reordering processes. Such software can analyze trends and forecast demand, enabling businesses to make informed decisions about their inventory.
- Train Staff: Ensure that all team members understand inventory management principles and procedures to maintain a culture of accountability and efficiency. Regular training sessions can keep staff updated on best practices and new technologies, fostering a knowledgeable workforce.
Tools for Effective Inventory Monitoring
Successful inventory monitoring relies on the right set of tools and technologies. Solutions range from comprehensive inventory management software packages to simpler tools like spreadsheets. The choice of tools often depends on the size of the business and the complexity of its inventory needs.
Popular options include:
- ERP Systems: Integrated systems that manage all aspects of a business, including inventory, finance, and supply chain management. These systems provide a holistic view of operations, allowing for better coordination and efficiency.
- Cloud-Based Inventory Solutions: Offer accessibility from anywhere and real-time updates, allowing for superior flexibility. These solutions are particularly beneficial for businesses with multiple locations or those that operate remotely.
- Barcode Scanners: Simplify inventory tracking and help reduce human error in data entry. By scanning items during receiving and shipping, businesses can maintain accurate records and streamline their inventory processes.
Utilizing these tools can significantly improve inventory visibility, ensuring that businesses maintain optimum stock levels. In addition to these technologies, adopting a regular auditing process can further enhance inventory accuracy. Conducting periodic physical counts and reconciling them with recorded data helps identify discrepancies and allows for timely corrections. Furthermore, integrating customer feedback into inventory management can provide valuable insights into purchasing trends, enabling businesses to adjust their stock levels in response to changing consumer demands.
How Technology Supports Optimal Stock Management
Technology plays a pivotal role in modern inventory management. By harnessing innovative solutions, businesses can streamline operations and improve overall efficiency.
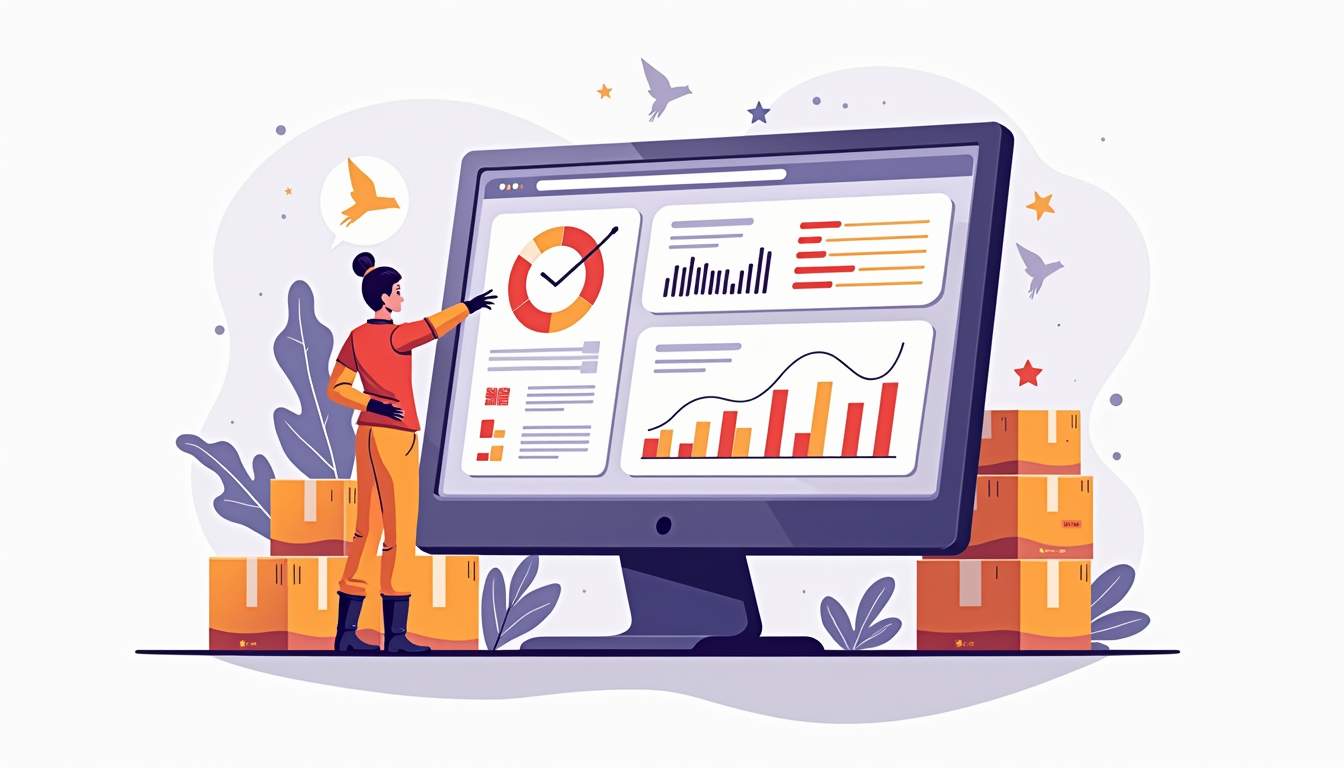
Advanced analytics, machine learning, and automation are just a few ways technology facilitates optimal stock management, enabling smarter decision-making and agility in response to market demands. Moreover, the integration of Internet of Things (IoT) devices allows for real-time tracking of inventory levels, providing businesses with immediate insights into stock availability and helping to prevent stockouts or overstock situations.
Generating SKU Numbers Using Excel Templates
Stock Keeping Units (SKU) are essential in the organization and management of inventory. Using Excel templates for generating SKU numbers can help streamline this process.
Businesses can create customized templates designed to assign unique SKU numbers based on product characteristics such as size, color, or type. This enhances inventory tracking by making items easily identifiable and searchable. Furthermore, by incorporating formulas and macros into these templates, companies can automate the SKU generation process, reducing human error and saving valuable time that can be redirected toward other critical areas of the business.
Effective Inventory Management Techniques for Direct-to-Consumer Stores
Direct-to-consumer (DTC) businesses face unique challenges in inventory management due to the fast pace of e-commerce. Implementing effective techniques such as drop shipping, where items are shipped directly from suppliers, can alleviate pressure on stock levels.
Additionally, employing a transparent return policy and accurate demand forecasting tools can help DTC stores manage inventory more dynamically, ensuring availability without overstocking. Utilizing customer data analytics to understand purchasing patterns can further refine inventory strategies, allowing businesses to anticipate trends and adjust stock levels accordingly. This proactive approach not only enhances customer satisfaction but also optimizes cash flow by minimizing excess inventory.
The Importance of Batch Production in Manufacturing
Batch production is an important technique in manufacturing that minimizes waste and optimizes resource allocation. By producing goods in batches based on forecasted demand, manufacturers can align production closely with market requirements.
This approach allows for more accurate inventory control and can contribute to maintaining optimum stock levels, thus reducing excess inventory and associated costs. Additionally, batch production can facilitate easier quality control, as manufacturers can test a sample from each batch before full-scale distribution. This not only ensures product consistency but also helps in identifying potential issues early in the production process, thereby safeguarding the brand's reputation.
Exploring Make to Stock: Pros and Cons
Make to stock (MTS) is a traditional production strategy focused on producing goods based on anticipated demand. One advantage of MTS is the ability to benefit from economies of scale, often resulting in lower per-unit costs.
However, the downside is the risk of overproduction. If demand forecasts are inaccurate, excess inventory can accumulate, leading to increased holding costs. Hence, while MTS can enhance efficiency, it is vital to combine it with accurate demand forecasting techniques. Implementing just-in-time (JIT) inventory practices alongside MTS can help mitigate these risks by ensuring that production schedules are closely aligned with actual demand, thereby reducing the likelihood of surplus stock and enhancing overall operational agility.
Inventory Control: An Overview
Effective inventory control is essential for any business looking to optimize its stock levels. It involves managing inventory keeping in mind several factors, including demand, costs, and lead times.
Proper inventory control enhances cash flow, reduces waste, and improves customer satisfaction by ensuring that products are available when needed. By maintaining an accurate inventory, businesses can avoid overstocking, which ties up capital, and understocking, which can lead to missed sales opportunities and dissatisfied customers.
Methods and Approaches to Effective Inventory Control
Different methods exist for managing inventory, including the Economic Order Quantity (EOQ) model, which calculates the ideal order size that minimizes total inventory costs. Another method is the Just-In-Time (JIT) approach, focusing on aligning inventory levels with actual consumption to reduce waste. This method requires a close relationship with suppliers to ensure timely deliveries, which can be challenging but ultimately beneficial for reducing excess stock.
Implementing Cycle Counting—a regular audit of a portion of the inventory rather than a full physical count—can help maintain accurate stock levels while minimizing disruptions to operations. This method allows businesses to identify discrepancies in inventory records more frequently and address issues proactively, leading to improved accuracy over time.
Additionally, leveraging technology such as inventory management software can significantly enhance the effectiveness of these methods. These tools provide real-time data analytics, enabling businesses to forecast demand more accurately and make informed decisions about stock replenishment. By integrating such technologies, companies can streamline their inventory processes, reduce human error, and ultimately improve their overall operational efficiency.
Through a combination of these techniques and strategies, businesses can achieve superior inventory control, keeping optimum stock levels aligned with customer demand and operational efficiency. The key is to remain adaptable and continuously assess inventory practices, ensuring they evolve alongside market trends and consumer behavior.