A Comprehensive Guide to Warehouse Management: Definitions and Essential Tools
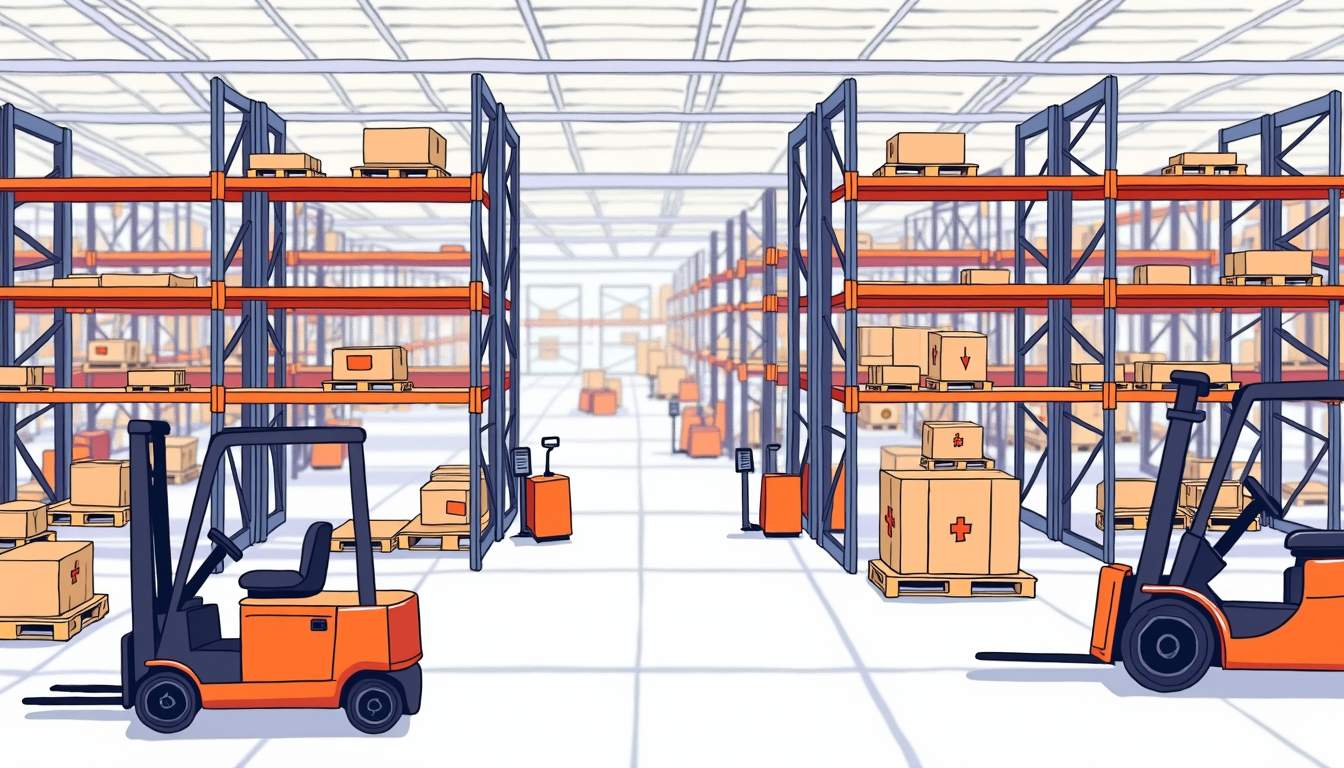
In today’s fast-paced market, effective warehouse management is crucial for businesses aiming to streamline operations and enhance efficiency. This comprehensive guide will help illuminate key concepts, tools, and practices within the field of warehouse management, making it easier for you to optimize your storage and distribution processes.
Understanding Warehouse Management: Key Definitions and Tools
Warehouse management encompasses the processes and operations involved in managing warehouse functions, from the receipt of products to their storage and eventual dispatch to customers. Successful warehouse management is not only about storing goods but also about optimizing the flow of goods in and out of a facility. This involves a careful balance of logistics, inventory control, and workforce management, ensuring that every aspect of the warehouse operates in harmony to meet customer demands swiftly and accurately.
Central to these operations are various tools and technologies designed to assist in tracking products, managing inventory, and enhancing productivity. An understanding of both essential definitions and tools is vital to mastering warehouse management. With the rise of e-commerce and the increasing complexity of supply chains, the role of effective warehouse management has never been more critical. As businesses strive to meet the expectations of fast delivery and real-time inventory visibility, the integration of advanced technologies becomes a necessity rather than a luxury.
Essential Tools for Effective Warehouse Management
Several tools help streamline warehouse operations. Some of the most essential include:
- Warehouse Management Systems (WMS): Software that facilitates and optimizes warehouse functionality through real-time tracking, inventory management, and process automation. A robust WMS can provide insights into inventory levels, order status, and even forecast demand, allowing managers to make informed decisions.
- Barcode Scanners: Devices that read barcodes on products to ensure accurate inventory tracking and minimize human error. These scanners can be handheld or fixed, and they significantly speed up the process of receiving and shipping goods, reducing the time spent on manual data entry.
- Automated Picking Systems: Technologies such as robotic pickers that improve efficiency and accuracy during the order fulfillment process. These systems can operate around the clock, increasing throughput and allowing human workers to focus on more complex tasks that require critical thinking and problem-solving skills.
- Storage Solutions: Racking systems and shelving units that maximize space utilization and streamline product retrieval. Innovative storage solutions, such as dynamic shelving and automated storage and retrieval systems (AS/RS), can adapt to changing inventory needs and help maintain an organized warehouse environment.
Utilizing these tools effectively can significantly enhance overall operational efficiency, contributing to better service delivery and customer satisfaction. Furthermore, the integration of data analytics within these tools allows warehouse managers to identify trends, optimize routes for picking and packing, and reduce waste, ultimately leading to a more sustainable operation. As technology continues to evolve, staying abreast of the latest advancements in warehouse management tools will be essential for businesses aiming to maintain a competitive edge in the marketplace.
Distinguishing Between Warehouse Management and Inventory Management
While warehouse management and inventory management may seem synonymous, they refer to different processes within the supply chain. Understanding these distinctions is essential for anyone involved in supply chain operations.
Key Differences Explained
Warehouse management focuses on the physical storage of goods and the efficient functioning of warehouse operations, including logistics, personnel, and equipment management. Conversely, inventory management encompasses broader aspects, such as product purchasing, tracking inventory levels, forecasting demand, and minimizing stock-outs.
Essentially, while warehouse management deals with the 'where' and 'how' goods are stored and retrieved, inventory management answers 'what' is available, 'how much' is needed, and 'when' to reorder. Both are integral to operating a successful supply chain.
Moreover, warehouse management systems (WMS) often utilize advanced technologies such as barcode scanning and RFID tracking to streamline operations and enhance accuracy in inventory handling. These systems help in managing the physical space of the warehouse, ensuring optimal layout and organization, which can significantly reduce the time taken for picking and packing orders. On the other hand, inventory management systems (IMS) are designed to provide insights into stock levels, turnover rates, and demand trends, allowing businesses to make informed purchasing decisions and maintain an optimal inventory turnover ratio.
Furthermore, the interplay between warehouse and inventory management is crucial for maintaining a competitive edge in today’s fast-paced market. For example, effective inventory management can lead to better warehouse efficiency by minimizing excess stock and ensuring that popular items are readily available. This synergy not only enhances customer satisfaction through timely deliveries but also reduces costs associated with overstocking and storage. As e-commerce continues to grow, the importance of integrating these two management processes becomes even more pronounced, as businesses strive to meet customer expectations while optimizing their operational capabilities.
The Importance of a Warehouse Management System
A Warehouse Management System (WMS) is a foundational tool that supports the logistics of any warehouse operation. It provides a framework for managing various tasks efficiently, ensuring that operations run smoothly. In today's fast-paced market, where consumer expectations are higher than ever, the role of a WMS becomes increasingly critical. It not only streamlines processes but also integrates seamlessly with other systems, such as Transportation Management Systems (TMS) and Enterprise Resource Planning (ERP) software, creating a cohesive operational environment.
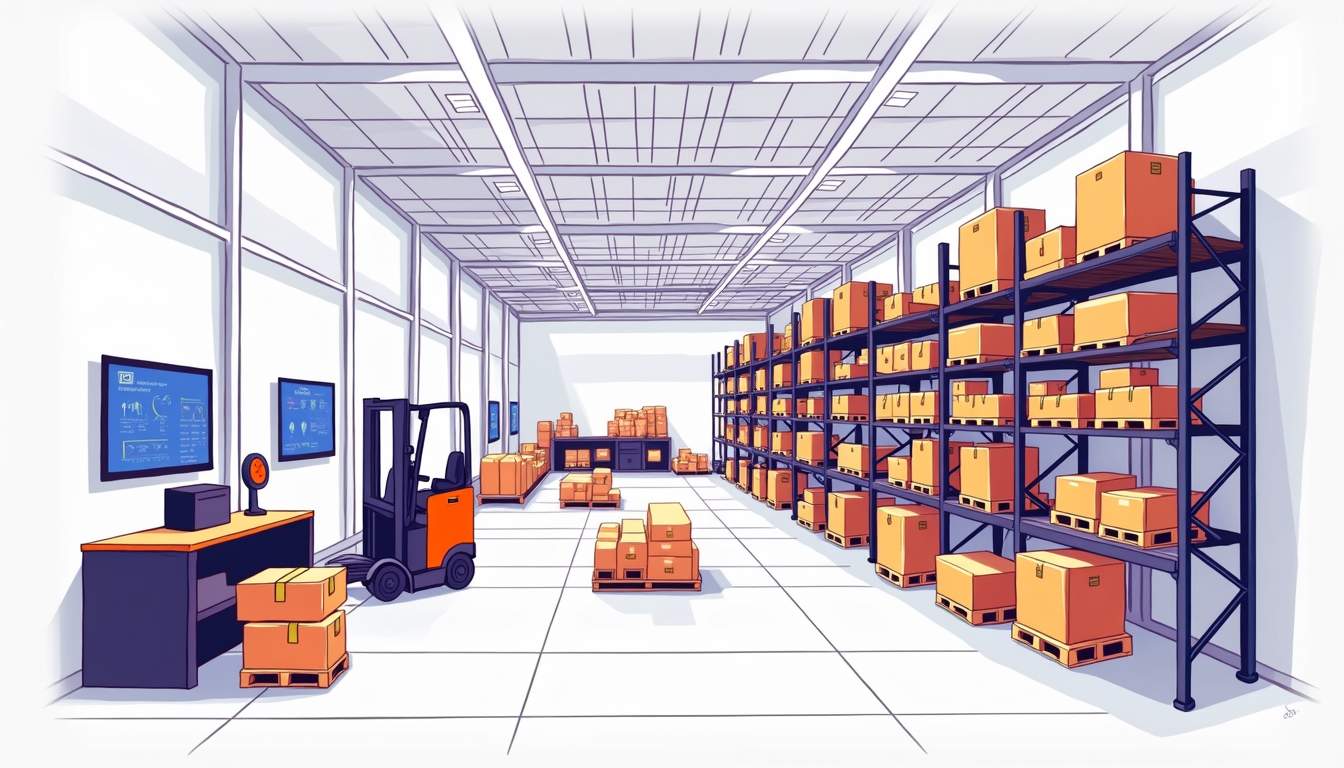
Benefits of Implementing a Warehouse Management System
Implementing a robust WMS offers numerous benefits:
- Improved Accuracy: Greater precision in tracking inventory shipments reduces errors and enhances customer satisfaction.
- Efficient Space Utilization: WMS assists in maximizing storage space through strategic placement and organization of products.
- Real-Time Data: Access to real-time inventory data allows for informed decision-making and better demand forecasting.
- Enhanced Productivity: Automation of various tasks decreases manual labor and increases overall efficiency.
As businesses evolve, incorporating such systems can provide a competitive edge in the market. Moreover, a WMS can facilitate better workforce management by providing insights into employee performance and workflow bottlenecks. By analyzing these metrics, managers can make data-driven decisions to optimize labor allocation and improve training programs, ultimately leading to a more skilled workforce.
Additionally, the integration of advanced technologies such as Artificial Intelligence (AI) and Internet of Things (IoT) within WMS can further enhance operational capabilities. For instance, AI algorithms can predict inventory needs based on historical data and trends, while IoT devices can monitor equipment health and track inventory movement in real time. This synergy not only boosts operational efficiency but also enables businesses to respond swiftly to market changes, ensuring they remain agile and competitive in a dynamic landscape.
Key Functions of a Warehouse Management System
A WMS consists of several functions that help streamline warehouse operations. These functions cover a wide range of activities that contribute to a well-oiled supply chain.
Streamlining Operations with WMS Features
The core features of a Warehouse Management System typically include:
- Receiving and Putaway: The system helps track incoming shipments and directs where products should be stored.
- Inventory Tracking: Real-time monitoring of stock levels ensures that businesses know exactly what is available at all times.
- Order Fulfillment: Efficient picking and packing processes ensure that customer orders are processed rapidly and accurately.
- Shipping: Smooth coordination of shipping schedules minimizes delays and helps meet customer expectations.
These features working in harmony result in enhanced operational efficiency, cost reduction, and improved service levels.
In addition to these core functionalities, advanced WMS solutions often incorporate sophisticated technologies such as barcode scanning and RFID tracking. These technologies not only improve accuracy in inventory management but also significantly speed up the receiving and shipping processes. For instance, barcode scanning allows warehouse staff to quickly log items into the system, reducing the time spent on manual entry and minimizing human error. RFID technology takes this a step further by enabling automatic tracking of products as they move through the warehouse, providing real-time visibility and enhancing overall inventory control.
Moreover, modern WMS platforms are increasingly integrating with other supply chain management tools, such as Transportation Management Systems (TMS) and Enterprise Resource Planning (ERP) systems. This integration fosters better communication across different departments and streamlines the entire supply chain process. For example, when a sales order is placed, the WMS can automatically communicate with the TMS to arrange for the most efficient shipping method, ensuring that products are delivered to customers in a timely manner. This interconnectedness not only improves operational efficiency but also enhances customer satisfaction by providing a seamless experience from order placement to delivery.
Top Warehouse Management Systems on the Market
With a myriad of options available, selecting the right Warehouse Management System requires careful consideration of several factors. Businesses must assess their specific needs and the features that different systems offer. The right WMS can streamline operations, reduce costs, and improve service levels, making it a critical investment for any organization that relies on efficient inventory management.
Criteria for Choosing the Right WMS
When evaluating a WMS, consider the following criteria:
- Scalability: The system should grow with your business, adapting to increased volume without compromising performance.
- User-Friendliness: An intuitive interface enhances training and minimizes the learning curve for staff.
- Integration Capabilities: Ensure the system can integrate seamlessly with other business software, such as ERP or CRM solutions.
- Support and Training: Robust customer support and training resources are vital for effective implementation and ongoing management.
By aligning the WMS with the unique needs of the business, companies can enhance their operational efficiency and effectiveness. Additionally, it’s important to consider the system's reporting capabilities, as detailed analytics can provide insights into inventory turnover rates, order accuracy, and labor productivity, allowing businesses to make data-driven decisions that further optimize their warehouse operations.
Popular WMS Solutions Reviewed
Some popular Warehouse Management Systems on the market today include:
- NetSuite WMS: A cloud-based solution that offers seamless integration with supply chain processes.
- Fishbowl Inventory: A cost-effective solution designed for small to medium-sized businesses that focuses on inventory tracking and order fulfillment.
- SAP EWM: A robust tool suitable for larger enterprises seeking comprehensive warehouse management functionalities.
- Zoho Inventory: An easy-to-use inventory management solution ideal for e-commerce businesses.
These systems provide a range of functionalities that can significantly improve warehouse efficiency when properly executed. For instance, NetSuite WMS not only enhances inventory visibility but also automates various processes, reducing the likelihood of human error. Similarly, Fishbowl Inventory allows businesses to manage their stock levels in real-time, which is crucial for maintaining customer satisfaction in a fast-paced market. Furthermore, SAP EWM’s advanced features, such as labor management and slotting optimization, cater to complex warehouse operations, ensuring that large enterprises can maximize their productivity and resource allocation.
Generating SKU Numbers: A Step-by-Step Guide
Stock Keeping Units (SKUs) are essential for effective inventory management as they provide unique identifiers for each product. Generating SKU numbers can seem daunting, but it can be straightforward with a structured approach.
To begin with, it's important to understand the components that make up a well-structured SKU. Typically, a SKU should include information that is relevant to the product, such as the category, brand, size, and color. For instance, if you are selling t-shirts, your SKU could start with "TS" for t-shirts, followed by "BR" for brand, "M" for medium size, and "BL" for blue color. This systematic approach not only helps in organizing your inventory but also makes it easier for employees to locate items quickly. Additionally, incorporating meaningful codes can assist in identifying trends and managing stock levels more efficiently.
Moreover, consistency is key when generating SKU numbers. Establishing a standard format that everyone in your organization adheres to can significantly reduce confusion and errors. For example, if you decide to use a combination of letters and numbers, ensure that all team members are trained on how to create and interpret these codes. This uniformity is particularly beneficial as your business grows and you add more products to your inventory. Furthermore, consider using software tools or inventory management systems that can automate SKU generation, which not only saves time but also minimizes the risk of human error in the process.
Understanding Optimum Stock Levels
Determining the optimum stock level is vital to maintaining balance within your supply chain. This concept revolves around finding the sweet spot where stock is sufficient to meet demand without overstocking or understocking. Achieving this balance is crucial not only for operational efficiency but also for customer satisfaction, as it ensures that products are available when needed, thereby avoiding lost sales and dissatisfied customers.
How to Determine Your Optimum Stock Level
To determine optimum stock levels, consider the following steps:
- Demand Forecasting: Analyze historical sales data to predict future demand accurately.
- Lead Time Analysis: Understand the time it takes to replenish stock and factor this into your ordering process.
- Order Frequency: Establish how often products need to be ordered based on lead times and forecasted demand.
- Safety Stock Calculation: Maintain a buffer stock to prevent stock-outs during demand spikes or supply chain disruptions.
By carefully analyzing these factors, businesses can maintain optimum stock levels that enhance efficiency while minimizing costs. Additionally, it's important to regularly review and adjust these parameters as market conditions, consumer preferences, and supply chain dynamics evolve. For instance, seasonal trends can significantly impact demand forecasting, necessitating a more agile approach to inventory management.
Moreover, leveraging technology can greatly assist in determining optimum stock levels. Inventory management software can provide real-time data analytics, helping businesses make informed decisions quickly. These tools can automate the tracking of stock levels, alerting managers when it’s time to reorder and providing insights into which products are moving quickly and which are not. This data-driven approach not only streamlines operations but also fosters a proactive rather than reactive inventory strategy, ultimately leading to improved profitability and customer loyalty.
The Role of Batch Production in Manufacturing
Batch production is a manufacturing technique where products are made as specified groups or quantities. This method is widely employed for its efficiency in managing production lines. It is particularly beneficial for companies that need to produce a variety of products without committing to a full-scale production run for each item. By allowing manufacturers to switch between different products with relative ease, batch production supports a diverse product range while still maintaining a level of efficiency that can be critical in competitive markets.
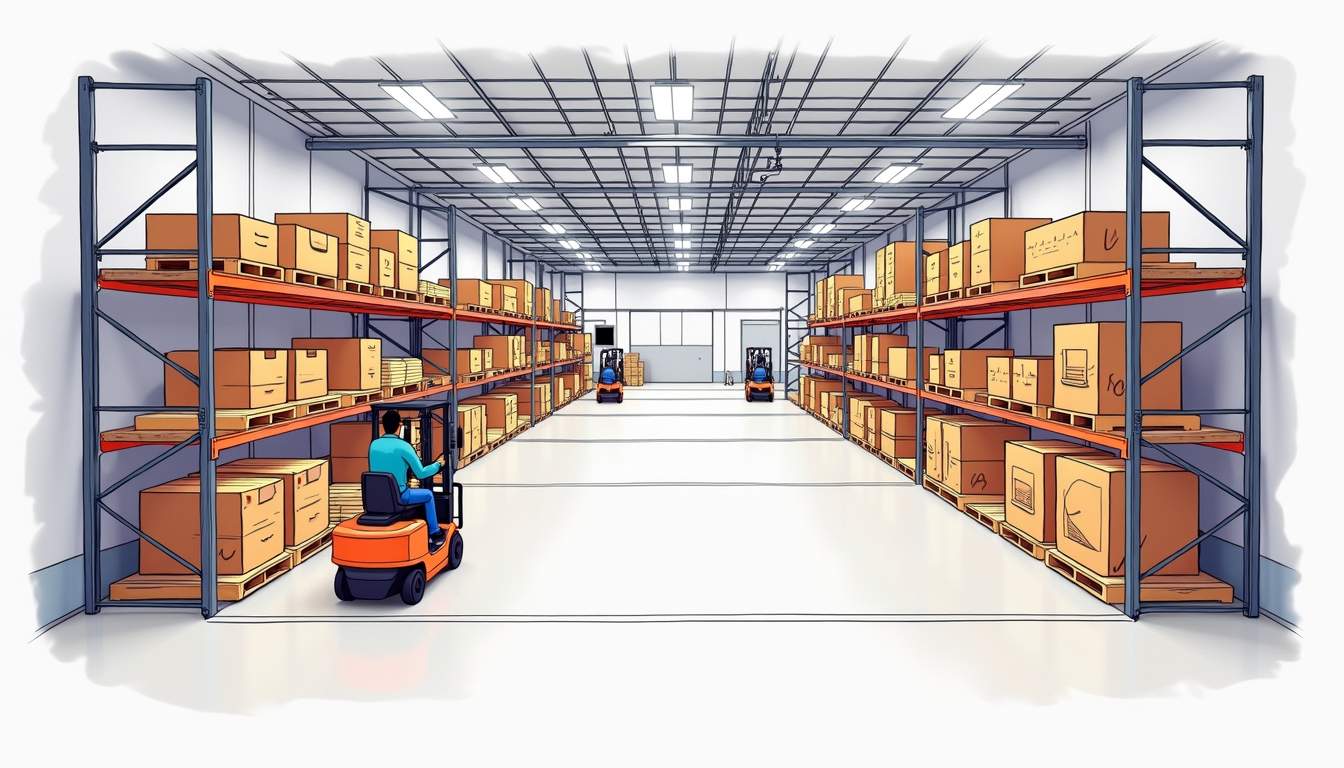
Advantages and Disadvantages of Batch Production
While batch production has several advantages, it also comes with its challenges. Here are some considerations:
- Advantages:
- Flexibility in production runs, allowing companies to respond to market demand.
- Lower setup costs due to amortization across multiple units produced.
- Ease of quality control since products are manufactured in groups.
- Disadvantages:
- Potential for inventory accumulation if demand forecasts are inaccurate.
- Possible cash flow issues due to the costs involved in batch production.
- Complexity in scheduling production runs and maintaining timelines.
For companies looking to enhance productivity while managing costs, understanding these advantages and disadvantages is crucial for decision-making. Additionally, the implementation of advanced technologies, such as automation and data analytics, can significantly mitigate some of the challenges associated with batch production. For instance, predictive analytics can improve demand forecasting, helping businesses minimize excess inventory and optimize production schedules. Moreover, automation can streamline setup processes, reducing downtime and enhancing overall efficiency.
In the context of batch production, the importance of skilled labor cannot be overstated. Workers must be adequately trained to handle the complexities of switching between different production runs and ensuring quality standards are met consistently. Investing in workforce development not only boosts productivity but also fosters a culture of continuous improvement, where employees are encouraged to identify inefficiencies and propose solutions. This collaborative approach can lead to innovative practices that enhance the batch production process and drive long-term success for manufacturing firms.