Essential Inventory Management Terms You Need to Know
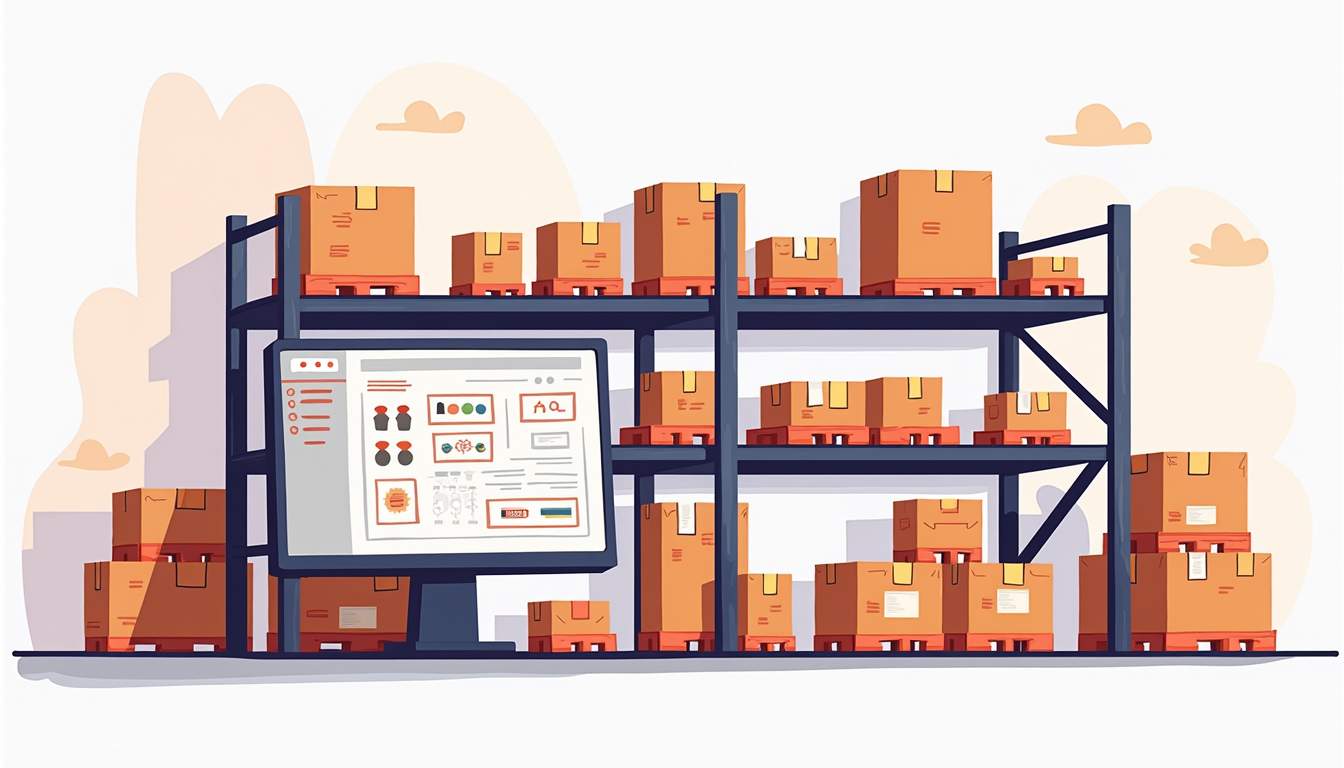
Inventory management is a crucial aspect of running a successful business. It not only ensures that you have the right products available at the right time but also helps manage costs and improve customer satisfaction. In this article, we will explore essential inventory management terms, their meanings, and how they can benefit your business. Whether you're a seasoned professional or a novice, understanding these terms will enhance your knowledge in the field.
Overview
At the heart of inventory management lies the concept of keeping track of your products, their quantities, and their movements. From managing stock levels to fulfilling customer orders, inventory management involves various processes that can significantly affect your bottom line. This section will introduce you to the fundamental elements of inventory management and set the stage for a deeper exploration of key terms and concepts.
Inventory management processes include receiving, storing, tracking, and distributing products. Each of these components plays a vital role in ensuring that your operations run smoothly. In this article, we will delve into specific terms that will arm you with the knowledge to make informed decisions about your inventory.
Understanding the intricacies of inventory management is essential for businesses of all sizes. For instance, effective inventory management can help reduce costs associated with overstocking or stockouts, which can lead to lost sales and dissatisfied customers. By employing techniques such as Just-In-Time (JIT) inventory, businesses can minimize holding costs while ensuring that products are available when needed. This balance is crucial, particularly in industries where demand can fluctuate rapidly, such as retail and e-commerce.
Moreover, technology plays an increasingly pivotal role in modern inventory management. With the advent of sophisticated inventory management software and tools, businesses can automate many of the processes involved, from tracking stock levels in real-time to generating detailed reports that provide insights into sales trends and inventory turnover rates. These advancements not only streamline operations but also empower businesses to make data-driven decisions, ultimately enhancing efficiency and profitability in a competitive marketplace.
Key Features
To effectively manage your inventory, it is essential to understand some key features that define successful inventory management systems. These features not only streamline your processes but also provide insights that can help drive your business strategy. A well-implemented inventory management system can significantly enhance operational efficiency, reduce costs, and improve customer satisfaction, making it a critical component of any successful business.
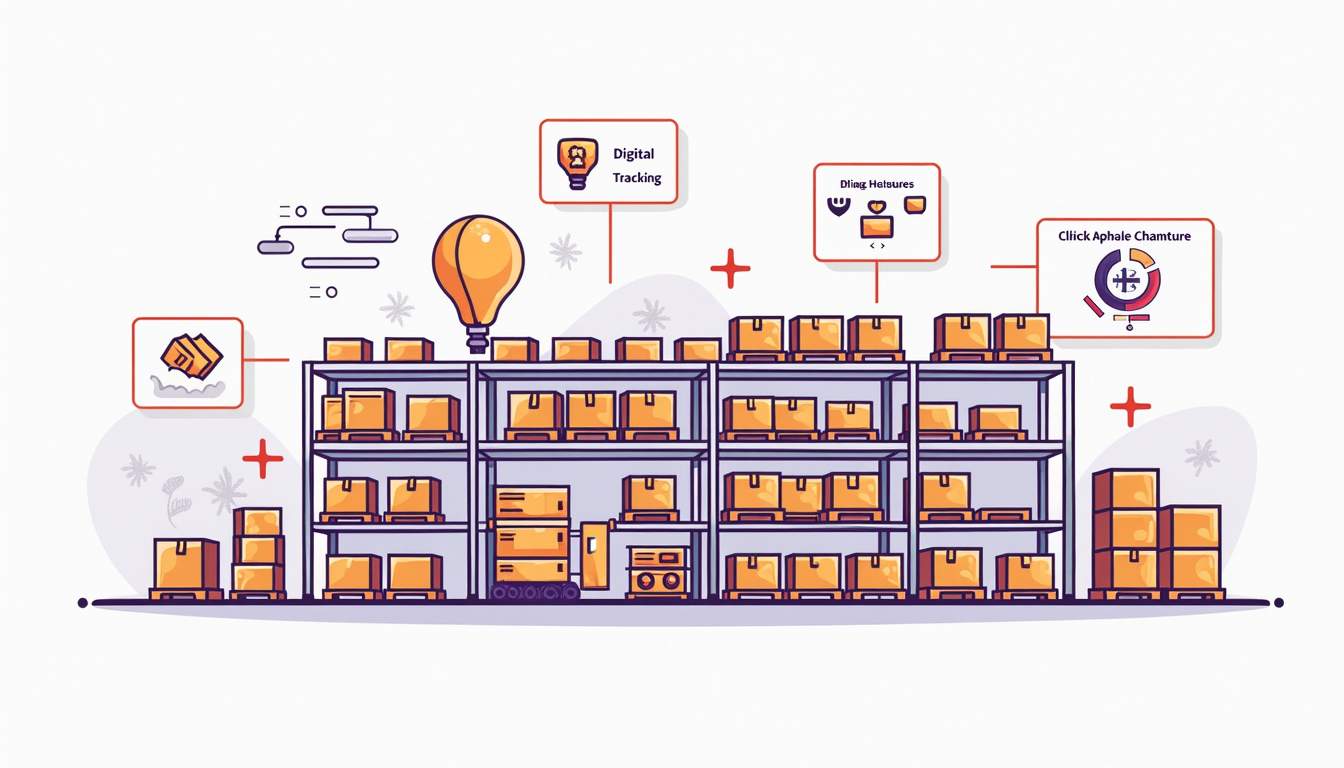
- Real-Time Tracking: This feature allows businesses to constantly monitor inventory levels, sales, and orders, ensuring optimal stock levels are maintained. By utilizing barcodes or RFID technology, companies can achieve precise tracking, minimizing the risk of stockouts or overstock situations that can lead to lost sales or increased holding costs.
- Reporting and Analytics: Reports provide valuable insights into sales trends, replenishment needs, and inventory turnover rates. Advanced analytics can also help identify seasonal patterns, enabling businesses to make informed decisions about purchasing and promotions, ultimately leading to improved profitability.
- Automation: Automation tools can help reduce human error and expedite processes such as ordering and reordering. By automating routine tasks, employees can focus on more strategic activities, such as analyzing inventory performance or enhancing customer relationships, which can lead to a more agile and responsive business environment.
- Mobile Accessibility: Cloud-based systems offer mobility, empowering teams to access inventory data from any location. This feature is particularly beneficial for businesses with multiple locations or remote teams, as it allows for seamless communication and collaboration across departments.
Understanding these key features will help you select an appropriate inventory management solution that meets your business’s specific needs. Additionally, it is crucial to consider the scalability of the system, as your inventory management requirements may evolve over time. A flexible solution can adapt to changes in your business model, whether that means accommodating new product lines, expanding into new markets, or integrating with other software tools to enhance overall functionality.
Moreover, the user interface and experience of the inventory management system play a significant role in its effectiveness. A well-designed interface can facilitate quicker training for staff, reduce the learning curve, and ultimately lead to higher adoption rates across your organization. The ability to customize dashboards and reports to fit your specific business metrics can also enhance user engagement and ensure that your team is consistently aligned with your strategic goals.
Seamless Integrations
In today's fast-paced business environment, the ability to integrate your inventory management system with other business applications is paramount. Seamless integrations can create a smooth workflow that enhances efficiency across different departments, from sales to accounting. By eliminating data silos, businesses can ensure that all teams have access to the same up-to-date information, which is essential for maintaining operational harmony.
When evaluating inventory management solutions, consider their ability to integrate with:
- Point-of-Sale (POS) Systems: Streamlining sales data directly into your inventory management system can provide real-time updates on stock levels. This immediate feedback loop helps prevent stockouts and overstock situations, allowing businesses to respond quickly to changing customer demands.
- E-commerce Platforms: Integration with platforms like Shopify or WooCommerce ensures your online inventory is in sync with your physical stock. This synchronization not only enhances customer satisfaction by providing accurate availability information but also optimizes your supply chain by reducing the risk of excess inventory.
- Accounting Software: Linking inventory data with your accounting system simplifies tracking profits and managing expenses. This integration allows for automated financial reporting, which can save time and reduce errors, enabling finance teams to focus on strategic planning rather than manual data entry.
These integrations can create a comprehensive view of your business operations, facilitating better decision-making. Furthermore, advanced integrations can also include Customer Relationship Management (CRM) systems, which allow businesses to analyze customer purchasing patterns and preferences. This data can be invaluable for tailoring marketing strategies and improving customer engagement. Additionally, integrating with supply chain management tools can enhance forecasting accuracy, ensuring that businesses are well-prepared for seasonal fluctuations and market trends. By leveraging these integrations, companies can not only streamline their operations but also gain a competitive edge in the marketplace.
Practical Use Cases
Understanding the practical applications of inventory management concepts can enhance your confidence in managing your stock. Here are some common use cases:
- Retail Management: Retailers using inventory management systems can ensure they always have high-demand products in stock, minimizing lost sales. By leveraging real-time data analytics, they can predict trends and adjust their stock levels accordingly, ensuring that popular items are always available for customers. This not only improves customer satisfaction but also enhances brand loyalty, as shoppers are more likely to return to a store that consistently meets their needs.
- Manufacturing: Manufacturers can better manage raw materials and finished goods, aligning production with demand. With the integration of just-in-time (JIT) inventory practices, manufacturers can reduce holding costs and minimize excess inventory. This approach allows for a more agile response to market fluctuations, enabling companies to ramp up or scale down production based on real-time sales data, thus optimizing resource allocation and reducing waste.
- Food and Beverage: These businesses often deal with perishable goods, so effective inventory management can reduce waste and ensure quality. Implementing first-in, first-out (FIFO) practices helps in maintaining freshness, while advanced tracking systems can alert managers to items nearing their expiration dates. Additionally, seasonal demand forecasting can assist in planning for peak periods, ensuring that popular items are well-stocked without over-purchasing that could lead to spoilage.
These examples illustrate how the proper inventory management approach can lead to significant improvements in efficiency and profitability. Furthermore, the adoption of technology such as automated inventory tracking systems and mobile inventory management apps can streamline operations even further. These tools not only provide real-time visibility into stock levels but also facilitate better communication across departments, ensuring that sales, procurement, and warehouse teams are all aligned. As businesses continue to evolve, the integration of artificial intelligence and machine learning into inventory management systems is set to revolutionize how companies forecast demand and manage their supply chains, paving the way for even greater efficiencies.
Relevant Industries
Inventory management is not restricted to one specific industry. Its principles can be applied across various sectors, each benefiting in unique ways from effective inventory practices.
- Retail: This includes clothing stores, supermarkets, and online shops, all of which require careful stock management. Retailers must analyze consumer trends and seasonal demands to optimize their inventory levels, ensuring that they have the right products available at the right time, while also minimizing excess stock that can lead to markdowns.
- Manufacturing: From raw materials to finished goods, managing inventory is critical for production efficiency. Manufacturers often employ just-in-time (JIT) inventory systems to reduce holding costs and improve cash flow, allowing them to respond swiftly to changes in demand without overproducing.
- Healthcare: Hospitals and pharmacies must manage medical supplies, which can impact patient care directly. Effective inventory management in healthcare not only ensures that essential medications and equipment are available when needed but also helps in tracking expiration dates and compliance with regulatory standards.
- Logistics: Companies involved in shipping and warehousing handle significant volumes of inventory that need precise management. Efficient logistics operations rely on sophisticated inventory tracking systems to monitor stock levels in real-time, facilitating timely deliveries and reducing the risk of stockouts.
Different industries may use varying tools and techniques, but the underlying principles of inventory management remain critical across the board. For instance, technology plays a vital role in modern inventory management, with many businesses adopting advanced software solutions that integrate with their existing systems to provide real-time data analytics and forecasting capabilities. This allows companies to make informed decisions about stock replenishment and to identify trends that can drive sales and improve customer satisfaction.
Moreover, the rise of e-commerce has transformed inventory management practices across sectors. Retailers must now consider not only their brick-and-mortar inventory but also their online stock levels, necessitating a seamless integration between physical and digital inventory systems. This complexity requires businesses to adopt agile inventory strategies that can adapt to fluctuating consumer behaviors and supply chain disruptions, ensuring they remain competitive in a fast-paced market.
1. Managing Inventory
Managing inventory is a systematic approach that involves overseeing the flow of goods from manufacturers to warehouses and from these facilities to the point of sale. It encompasses various activities, including order fulfillment, stock replenishment, and demand forecasting.
Effective management reduces excess stock and improves cash flow while ensuring that products are available for customers when needed. Utilizing modern inventory management systems can make this task easier and more streamlined.
In today's fast-paced retail environment, the importance of real-time inventory tracking cannot be overstated. Businesses that implement technologies such as RFID (Radio Frequency Identification) and barcode scanning can gain immediate insights into stock levels, helping to prevent stockouts and overstock situations. This not only enhances customer satisfaction but also optimizes storage space and reduces carrying costs, allowing businesses to allocate resources more effectively.
Moreover, integrating inventory management with other business operations, such as sales and customer relationship management, can provide a holistic view of performance. This interconnectedness enables companies to analyze trends and make data-driven decisions that align inventory levels with consumer demand. By leveraging advanced analytics and machine learning algorithms, businesses can predict future inventory needs with greater accuracy, ensuring they remain competitive in an ever-evolving marketplace.
2. Understanding Stock Keeping Units (SKUs)
Stock Keeping Units, or SKUs, are unique identifiers assigned to each product in your catalog. These codes allow businesses to easily track their inventory levels, sales patterns, and product performance. Each SKU can contain information such as product type, size, color, and other attributes that help differentiate products. For instance, a clothing retailer might use SKUs that indicate not only the type of garment but also its size and color, such as "SHIRT-M-RED" for a medium-sized red shirt. This granularity in SKU design helps in quickly identifying specific items, facilitating smoother operations in both physical and online stores.
By understanding SKUs, businesses can optimize their ordering processes, ensure accurate inventory counts, and make informed decisions about product discontinuations. Moreover, the use of SKUs can significantly enhance the efficiency of supply chain management. When businesses have a clear view of their inventory through SKUs, they can better forecast demand, reduce excess stock, and minimize the risk of stockouts. This not only leads to cost savings but also improves customer satisfaction, as products are more likely to be available when needed. Additionally, integrating SKU data with sales analytics can provide insights into which products are performing well and which may need adjustments in marketing or pricing strategies.
3. Analyzing Inventory Turnover
Inventory turnover is a key performance indicator that measures how quickly inventory is sold and replaced over a specific period. Analyzing turnover rates provides insights into product demand, selling strategies, and stock management efficiency.
A high turnover rate typically indicates strong sales, whereas low rates may signal overstocking or declining product interest. Businesses can use this data to adjust purchasing and marketing strategies accordingly.
Moreover, understanding the nuances of inventory turnover can lead to more informed decision-making. For instance, seasonal products may exhibit fluctuating turnover rates throughout the year, necessitating a keen analysis of historical sales data to forecast future demand accurately. Retailers often find that certain items sell faster during specific times, such as holidays or back-to-school seasons, which can significantly influence inventory management practices. By leveraging this information, businesses can optimize their stock levels, ensuring they have enough products on hand to meet demand without tying up excessive capital in unsold inventory.
Additionally, businesses should consider the impact of external factors on inventory turnover. Economic conditions, competitive landscape changes, and shifts in consumer preferences can all affect how quickly products move off the shelves. For example, during an economic downturn, consumers may prioritize essential goods over luxury items, leading to a noticeable change in turnover rates across different product categories. By staying attuned to these external influences, businesses can adapt their strategies in real time, ensuring they remain agile and responsive to market dynamics.
4. Calculating Lead Time
Lead time refers to the amount of time it takes for an order to be fulfilled from the moment it is placed until the product is received. It encompasses all processes involved, including sourcing, manufacturing, and shipping.
Calculating lead time is crucial for accurate demand forecasting and ensuring that inventory levels are optimized. Understanding this metric helps businesses mitigate stockouts and improve customer satisfaction.
To accurately calculate lead time, businesses must consider various factors that can influence the duration of each phase. For instance, the sourcing phase may vary significantly depending on supplier reliability and the distance from which materials are procured. Additionally, manufacturing times can fluctuate based on production capacity, workforce availability, and even equipment efficiency. By analyzing historical data and trends, companies can better predict lead times and adjust their operations accordingly.
Moreover, shipping times can be affected by external factors such as weather conditions, transportation delays, and customs clearance processes. In today's global marketplace, where many businesses rely on international suppliers, understanding the complexities of shipping logistics becomes even more essential. Implementing advanced tracking systems and maintaining open lines of communication with logistics partners can further enhance the accuracy of lead time calculations, allowing businesses to respond proactively to any potential delays.
5. Determining Reorder Points
Reorder points are predefined inventory levels at which new stock should be ordered to avoid running out. Determining these points involves analyzing sales trends and lead times to balance stock availability and excess inventory.
By accurately calculating reorder points, businesses can maintain optimal inventory levels, reducing the risk of lost sales due to stockouts while minimizing carrying costs.
6. Addressing Stockouts
Stockouts occur when inventory levels fall to zero for a particular product. This situation can lead to lost sales and dissatisfied customers. To address stockouts, businesses can implement inventory management strategies such as regular stock audits and automated inventory replenishment systems.
Proactive measures, including accurate demand forecasting and maintaining safety stock levels, can help in preventing stockouts effectively.
7. Establishing Safety Stock Levels
Safety stock refers to extra inventory kept on hand to prevent stockouts during unexpected demand surges or supply chain delays. Establishing appropriate safety stock levels is essential for creating a buffer against uncertainty in demand and supply.
Evaluating historical sales data, lead times, and variability in demands assists in calculating the right amount of safety stock to maintain, ultimately safeguarding your operations.
8. Evaluating Carrying Costs
Carring costs are the total costs incurred to hold inventory over a specific period. These costs can include warehousing, insurance, spoilage, and administrative expenses. Evaluating carrying costs is crucial for understanding the propensity of inventory to affect profitability.
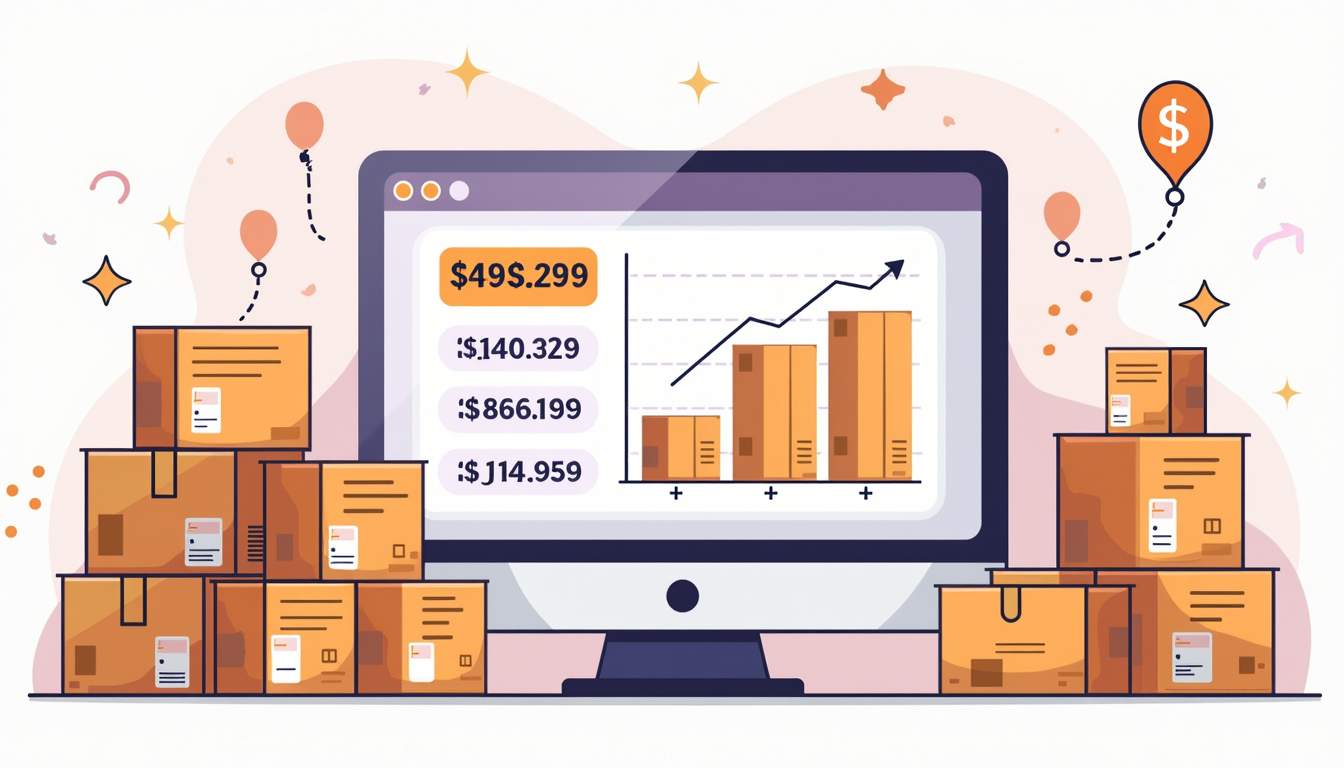
By closely monitoring carrying costs, businesses can make informed decisions about inventory levels, ensuring that they maintain a balance between having enough stock on hand and minimizing excess holding costs.
9. Optimizing Order Quantities
Optimizing order quantities involves determining the amount of product to order to minimize costs while meeting customer demand. This concept is essential for preventing overstocking and ensuring that inventory turnover rates remain healthy.
Often guided by various inventory control models, such as the Economic Order Quantity (EOQ) model, businesses can improve their ordering processes and achieve a more streamlined supply chain.
10. Approaches to Inventory Valuation
Inventory valuation is the process of assigning monetary value to the inventory a business holds. Different methods, including FIFO (First-In, First-Out) and LIFO (Last-In, First-Out), can affect financial statements and taxation.
Understanding these approaches helps businesses accurately reflect their inventory on financial reports while making strategic decisions regarding pricing and production.
Mastering Inventory Management Techniques
Mastering inventory management techniques is essential for ensuring operational efficiency, customer satisfaction, and profitability. By focusing on key concepts such as those discussed in this article, businesses can develop effective strategies to manage and optimize their inventories.
From employing advanced technologies to utilizing process improvement methodologies, mastering inventory management techniques can create significant competitive advantages in the marketplace.
Overcoming Common Inventory Management Challenges
Despite the best plans, businesses often face challenges in inventory management. Some of these common challenges include demand fluctuations, misalignment between sales forecasts and stock levels, and supply chain disruptions.
Overcoming these challenges requires flexibility and the continuous evaluation of management strategies. Leveraging technology, such as inventory management software, can enhance visibility and control over inventory processes, enabling businesses to respond swiftly to changes in market conditions.
In conclusion, understanding essential inventory management terms is invaluable for any business looking to enhance its operations. By mastering these concepts, you can not only manage your inventory more effectively but also contribute to the overall success of your business.