Mastering Average Inventory Calculation: A Comprehensive Guide
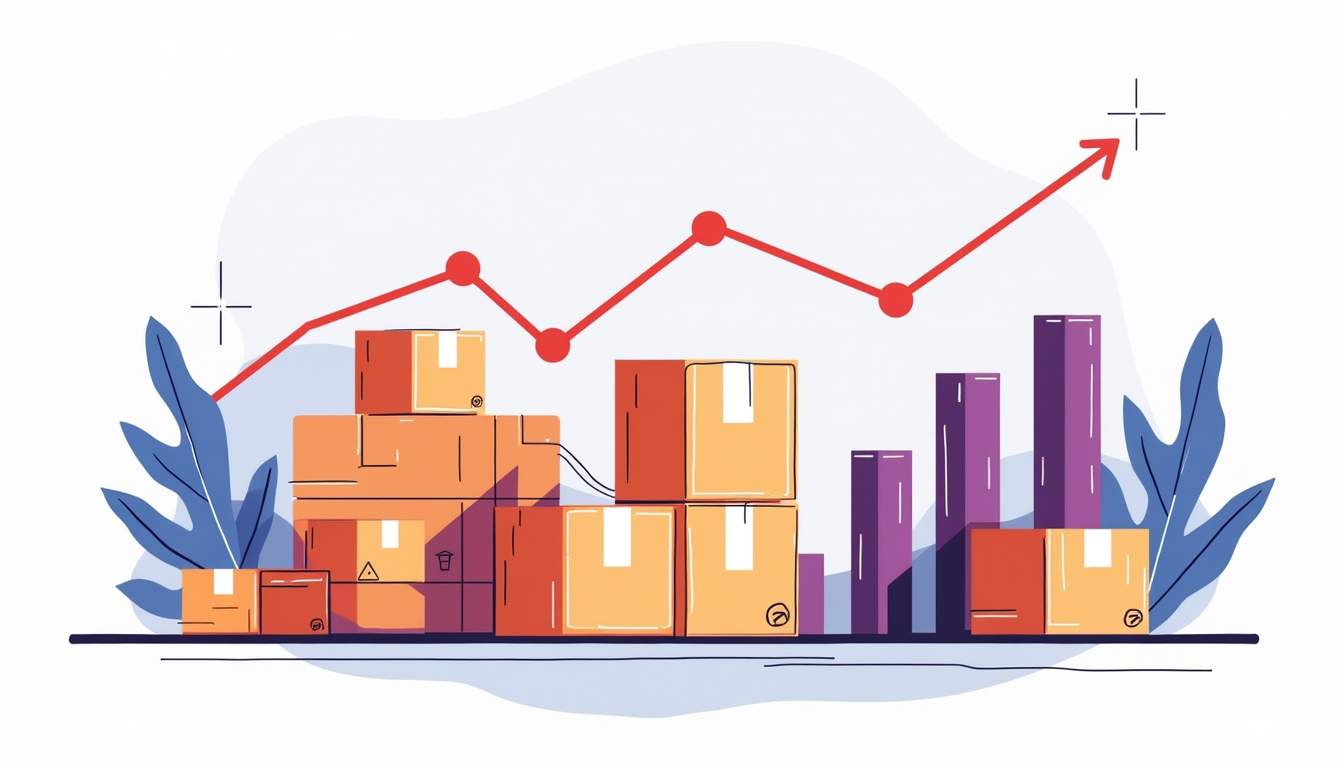
Average inventory plays a critical role in the financial health of a business, helping companies manage their stock effectively. This comprehensive guide aims to elucidate the intricacies of average inventory calculation, the concepts behind it, and its implications in various business scenarios.
Calculating Average Inventory: A Step-by-Step Guide
Understanding how to calculate average inventory is essential for businesses that deal with physical products. The average inventory provides valuable insights into how much stock a company typically has over a certain period, directly affecting profitability and cash flow management. By keeping a close eye on average inventory levels, businesses can optimize their supply chain processes, reduce holding costs, and improve overall operational efficiency.
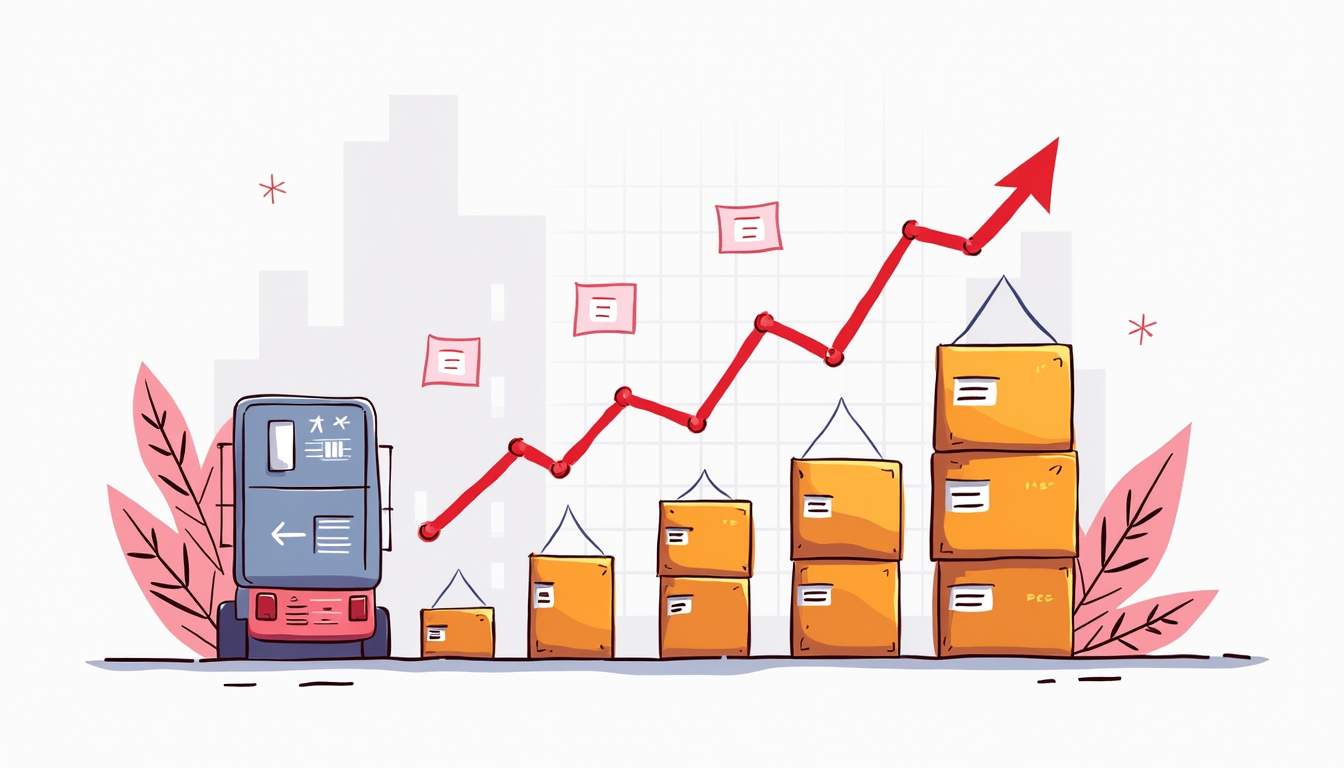
Understanding the Formula for Average Inventory
The formula for calculating average inventory is relatively straightforward: it involves taking the beginning inventory plus the ending inventory and dividing it by two. Thus, the formula can be expressed as follows:
Average Inventory = (Beginning Inventory + Ending Inventory) / 2
This simple calculation allows businesses to assess inventory levels effectively. However, businesses should be mindful of whether they are considering a specific time frame, such as monthly or yearly averages, to suit their operational needs. Additionally, companies may choose to use a weighted average method if they have significant fluctuations in inventory levels throughout the year, which can provide a more accurate picture of their inventory status.
Practical Examples of Average Inventory Calculations
Let's take a deeper dive into practical examples. Imagine a small retail business with a beginning inventory of $1,000 and an ending inventory of $1,500 at the end of the month. Using the formula, the average inventory would be:
Average Inventory = ($1,000 + $1,500) / 2 = $1,250
This average inventory figure helps the retailer gauge their stock availability and plan for future orders. Understanding these calculations can empower business owners to make wiser inventory-related decisions. For instance, if the retailer notices that their average inventory is consistently high, it may indicate overstocking issues, leading to increased holding costs, such as storage fees and potential obsolescence of products. Conversely, a low average inventory might suggest that the business is at risk of stockouts, which can lead to lost sales and dissatisfied customers.
Furthermore, businesses can enhance their inventory management practices by incorporating inventory turnover ratios alongside average inventory calculations. The inventory turnover ratio measures how many times inventory is sold and replaced over a specific period, providing insights into sales performance and inventory efficiency. By analyzing both average inventory and turnover rates, business owners can make informed decisions about purchasing, pricing strategies, and promotional activities to maximize profitability.
Defining Average Inventory: Key Concepts
Average inventory is not just a number; it reflects various aspects of business operations, from cash flow to inventory turnover rates. The nuances of this metric can inform many strategic business decisions. For instance, a high average inventory might suggest that a business is overstocked, which can tie up capital and lead to increased holding costs. Conversely, a low average inventory could indicate that a business is operating efficiently, but it may also raise concerns about potential stockouts and lost sales opportunities. Understanding the balance between these extremes is crucial for maintaining optimal inventory levels.
Average inventory also aids in calculating the inventory turnover ratio, which compares the cost of goods sold with the average inventory over a certain period. This ratio indicates how effectively a business is managing its stock and can highlight areas needing improvement. A higher turnover ratio typically signifies that a company is selling goods quickly and efficiently, while a lower ratio may point to overstocking or declining demand. Additionally, businesses can use this metric to benchmark against industry standards, allowing them to gauge their performance relative to competitors and identify best practices for inventory management.
Moreover, the calculation of average inventory can vary depending on the method used, such as the simple average, moving average, or weighted average. Each method has its own implications and can provide different insights into inventory management. For example, a moving average can smooth out fluctuations in inventory levels over time, making it easier to spot trends and make informed decisions. Understanding these methodologies is essential for businesses aiming to refine their inventory strategies and enhance overall operational efficiency.
Lastly, average inventory plays a significant role in financial forecasting and budgeting. By analyzing historical inventory data, businesses can better predict future inventory needs, align purchasing strategies, and optimize cash flow. This foresight is particularly beneficial in industries with seasonal demand fluctuations, where maintaining the right inventory levels can mean the difference between capitalizing on peak sales periods and facing excess stock during slower times. Thus, integrating average inventory analysis into broader financial planning can lead to more resilient and adaptable business operations.
Common Challenges with Average Inventory
While calculating average inventory seems easy, several challenges can arise. Misestimations in beginning or ending inventories can lead to inaccurately reported averages. Additionally, fluctuating inventory levels can complicate matters further. These fluctuations can be attributed to various factors, including seasonal demand variations, supply chain disruptions, and unexpected changes in consumer behavior. Businesses must be vigilant in monitoring these elements to ensure that their average inventory calculations reflect true operational realities.
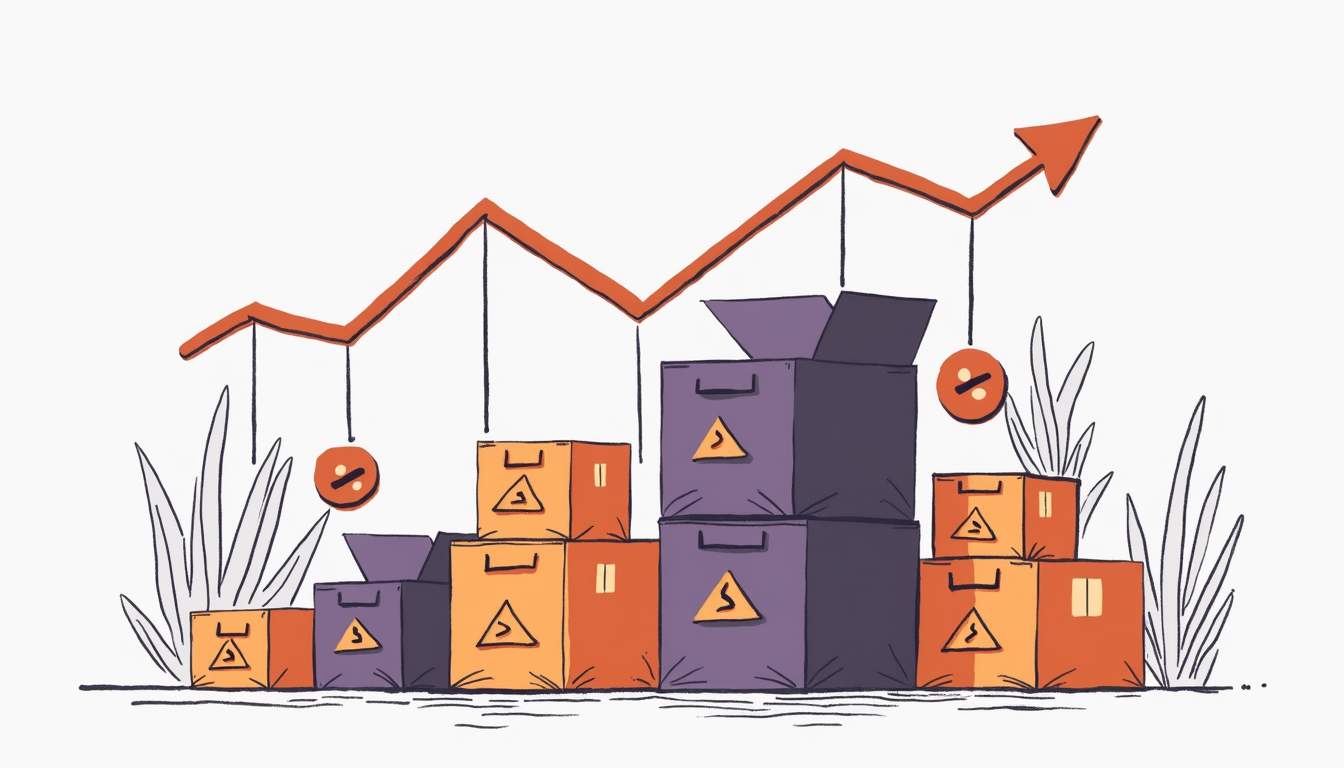
An Example: Imaginary Company’s Average Inventory at $1100
Consider an imaginary company, ABC Supplies, which operates efficiently but faces challenges due to vast fluctuations in its stock levels. In one quarter, they see a beginning inventory of $800 and an ending inventory of $1,400. Using the average inventory formula, their average inventory would be:
Average Inventory = ($800 + $1,400) / 2 = $1,100
While this figure is useful, ABC Supplies might want to implement more frequent evaluations of stock levels to improve their forecasting and purchasing strategies. By utilizing advanced inventory management software, they could gain insights into sales trends and inventory turnover rates, allowing for more informed decision-making. This proactive approach could mitigate the risks associated with stockouts or overstock situations, ultimately leading to enhanced customer satisfaction and improved cash flow.
Understanding Inventory Turnover: A Critical Metric
Inventory turnover is another valuable metric tied to average inventory. It indicates how many times a business sells and replaces its stock within a specific period. Achieving a healthy inventory turnover rate can help maintain liquidity and reduce storage costs. Businesses often aim for a turnover rate that aligns with their industry standards, as this can vary significantly across sectors. For example, perishable goods may require a higher turnover rate compared to durable goods, which can remain in inventory for longer periods.
A high inventory turnover ratio might suggest strong sales and/or ineffective buying practices, leading to stock shortages. Conversely, a low turnover indicates that goods are not selling quickly, which can lead to excess inventory or outdated products. To address these issues, companies may need to adjust their pricing strategies, enhance marketing efforts, or even reconsider their product offerings to align better with customer preferences and market demands.
Creating SKU Numbers: Using Excel Templates
To effectively manage average inventory levels, businesses often use Stock Keeping Unit (SKU) numbers to track products meticulously. An effective way of managing SKUs is through templates in Excel, which can help streamline inventory tracking processes. These templates not only allow for easy data entry but also facilitate the generation of reports that can provide insights into sales patterns and inventory health.
Creating SKU numbers involves assigning a unique identifier to each product, making it easier to monitor stock levels and sales data. Excel templates can further simplify this task, allowing businesses to input data and automate calculations related to average inventory. Additionally, by incorporating features such as conditional formatting and pivot tables, businesses can visualize their inventory data more effectively, enabling quicker responses to changes in demand and enhancing overall inventory management efficiency. This level of organization is crucial for businesses aiming to maintain a competitive edge in today’s fast-paced market environment.
The Concept of Optimum Stock Level Explained
Optimum stock level refers to the ideal amount of inventory that a business should maintain to meet customer demand without excess. This concept helps in balancing costs associated with storing surplus inventory and potential lost sales due to stockouts.
Determining the optimum stock level requires understanding consumer trends, lead times, and the variability of sales patterns. Tools like demand forecasting software can aid businesses in refining their stock levels to maximize efficiency.
Moreover, the optimum stock level is not static; it can fluctuate based on seasonal trends, economic conditions, and changes in consumer preferences. For instance, a retail business may find that certain products sell more during holiday seasons, necessitating a temporary increase in stock levels to meet heightened demand. Conversely, during off-peak times, businesses may need to reduce their inventory to avoid the costs associated with overstocking. This dynamic nature of stock levels underscores the importance of continuous monitoring and adjustment.
Additionally, businesses can leverage advanced analytics and machine learning algorithms to predict future demand more accurately. By analyzing historical sales data, market trends, and even social media sentiment, companies can gain insights that inform their inventory decisions. This proactive approach not only helps in maintaining the optimum stock level but also enhances customer satisfaction by ensuring that popular products are readily available, thus fostering brand loyalty and repeat business.
The Role of Batch Production in Manufacturing
In manufacturing settings, batch production significantly influences average inventory calculations. This production method entails the manufacturing of a set quantity of goods simultaneously, after which another batch is prepared. The flexibility of batch production allows manufacturers to switch between different products with relative ease, making it a popular choice for companies that offer a diverse range of items. This adaptability is particularly beneficial in industries where consumer preferences can shift rapidly, requiring manufacturers to respond quickly to changes in demand.
Batch production affects average inventory as it tends to create periodic spikes in stock levels, which can complicate the calculations. Businesses must manage these spikes efficiently to avoid excess stock and ensure smooth operations. Effective inventory management practices, such as just-in-time (JIT) systems, can help mitigate the risks associated with batch production by minimizing the amount of inventory held at any given time. This approach not only reduces storage costs but also enhances cash flow, allowing companies to allocate resources more strategically.
Exploring the Make to Stock Strategy: Pros and Cons
The make to stock strategy aligns closely with average inventory management. In this approach, products are manufactured based on anticipated demand, enabling companies to keep consistent stock levels. While it can lead to high customer satisfaction, it also requires accurate forecasting to avoid overproduction. This reliance on forecasting means that businesses must invest in sophisticated analytics and market research tools to predict trends accurately, which can be a significant upfront cost but pays off in the long run through improved efficiency and customer service.
The pros of the make to stock strategy include faster fulfillment rates and the ability to meet customer demand promptly. However, the cons often consist of potential overproduction, leading to excess inventory and storage costs if demand does not materialize as anticipated. Additionally, companies may face challenges related to product obsolescence, particularly in fast-moving consumer goods markets where trends change rapidly. As a result, businesses must strike a delicate balance between maintaining sufficient stock levels to satisfy customer needs and avoiding the pitfalls of overproduction that can erode profit margins.
Inventory Control: Overview and Techniques
Effective inventory control is essential in mastering average inventory calculations. Businesses must adopt robust inventory management techniques to ensure their stock levels align with operating goals. This alignment not only helps in maintaining a steady flow of operations but also plays a critical role in minimizing costs associated with excess inventory and stockouts.
Inventory control encompasses various methods, including just-in-time (JIT) inventory, ABC analysis, and the economic order quantity (EOQ) model. These approaches help organizations manage their stock efficiently, maintain customer satisfaction, and enhance financial performance. By leveraging these techniques, businesses can create a responsive supply chain that adapts to market demands and customer preferences, ultimately leading to a competitive advantage.
Methods of Inventory Control: A Comprehensive Guide
Adopting effective inventory control methods can minimize the risks associated with average inventory miscalculations. JIT inventory focuses on reducing waste by receiving goods only as needed, thus lowering holding costs. This method not only streamlines operations but also fosters stronger relationships with suppliers, as businesses must communicate effectively to ensure timely deliveries.
ABC analysis categorizes inventory into three segments based on the importance of items, allowing businesses to focus efforts on managing high-value products effectively. This prioritization ensures that resources are allocated efficiently, maximizing the return on investment for the most critical items. Meanwhile, the EOQ model helps determine the ideal quantity to order to minimize costs, thus supporting average inventory management. By calculating the EOQ, businesses can strike a balance between ordering costs and holding costs, leading to improved cash flow and operational efficiency.
Getting Started with Inventory Management Basics
For businesses beginning their journey in inventory management, grasping the foundational principles is crucial. Start by conducting a thorough inventory assessment, identifying trends, and understanding turnover rates. This initial evaluation provides valuable insights into which products are performing well and which may require strategic adjustments.
By diving into the numbers, businesses can fully comprehend their average inventory levels and implement relevant strategies to optimize their stock management. Adequate training and the incorporation of technology can further enhance these efforts, paving the way for improved financial performance. Utilizing inventory management software can automate many processes, providing real-time data that aids in decision-making and forecasting. Additionally, regular audits and reviews of inventory practices can help identify areas for improvement, ensuring that businesses remain agile and responsive to changing market conditions.
In conclusion, mastering average inventory calculation and understanding its implications can greatly benefit businesses. By applying strategic calculations and inventory control methods, companies can not only enhance their operational efficiency but also ensure long-term success.